ANSI/ISEA Z358.1 Emergency Shower & Eye Wash Testing
Importance of Safe Water For Your Eyes By Hayden Del Dotto, Haws Online Content Specialist
Chances are that if your day involves using an emergency eyewash station, it probably hasn’t been the best of days. An issue with chemicals or hazardous substances in your eyes can ruin any day, but if you add an eyewash with non-sterile water to this equation it could ruin your life. According to OSHA, each day over 2,000 people injure their eyes at work and temporary or permanent vision loss is a result of 10%-20% of these occupational eye injuries. Loss of vision, whether it’s temporary or permanent, is a scary thing and along with a diminished quality of life, there are large costs for both an individual and employer. Direct costs for eye injuries alone cost employers over $467 million a year according to the U.S. Bureau of Labor Statistics (BLS).
To prevent such permanent and costly eye injuries it is important for an employer to not only have eyewashes, but also make sure that the water being used in them is safe as well. For the water to be safe it must be between 60°F and 100°F so that it does not enhance the chemical reaction in the eyes and is comfortable for the whole 15 minutes of use. Along with temperature, making sure that the eyewash water is ‘sterile’ is another important factor for safe water. If a portable eyewash doesn’t have ‘sterile’ preserved water, it could lead to additional irritation.
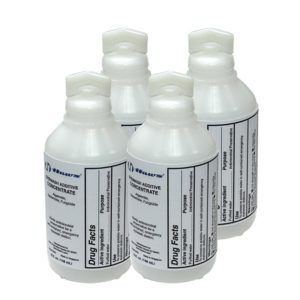
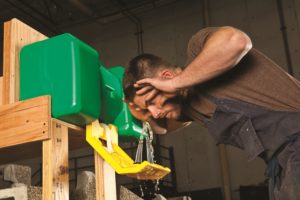
Bacteriostatic preservatives are an ideal solution to having ‘sterile’ preserved water in your self-contained, portable eyewashes because they limit the growth of bacteria in the water. One 5 oz. bottle of the Haws model 9082 will preserve five to twenty gallons of potable water for up to three months. This ‘sterile’ solution is in compliance with FDA regulations and is an important piece to your own safety as well as your employees’. Find out more about the model 9082 and more Haws products by visiting the website at: https://www.hawsco.com.
Irrigate eyes like medical pros [First seen in ISHN Magazine June 2018]
Introduce the flushing fluid at the inner corner of the eye
An injury can change life in an instant. According to the National Safety Council, occupational injuries occur every seven seconds in the United States. Luckily, through the years, stringent regulation and a growing concern for the health and well-being of employees has led to advancements in processes, safety procedures, and first aid protocols to treat the injured. This movement has had a profound impact on emergency equipment, including the eyewash industry. 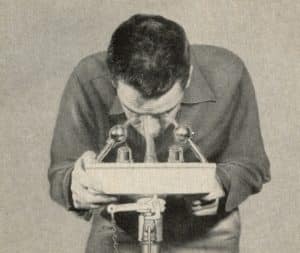
In the early 1900s, it was said that a well-known energy company created the first emergency eyewash by taking two bubbler heads from drinking fountains and mounting them on opposite sides of a sink facing each other with plumbing run to both of the heads (see photo). When activated, the water streams formed a double arch that directed water from the outer perimeter of the sink to the center. An injured victim would place their face into the double streams and irrigate both eyes simultaneously. It was a great concept and one that took the safety industry to a new level over the subsequent years.
Yet, as medical advancements continued to evolve, the eye irrigation process in emergency situations did not quite follow suite. Irrigating with water streams that contact the eye at its outer corner, or canthus, and flow inward toward the nose is diametrically opposed to the way medical professionals irrigate eyes.
Think about how you use eye drops. The general practice is to tilt the head back and place the dropper near the inner corner for the drops to drain to the outside of the eye and down the outside of your cheek.
The Lacrimal System
To comprehend the logic behind how the medical communitytreats eye contamination situations you first should understand the eye’s lacrimal system. The human eye is equipped with an automatic lubricating and cleansing mechanism, called the lacrimal system (see illustration). It consists of the lacrimal gland which produces tears, the ducts that channel tears from the lacrimal gland to the ocular surface, and the lacrimal puncta which are drains that channel excess fluids out of the ocular surface.
Importantly, the lacrimal puncta drain excess fluids directly into the nasal cavity. This process is the reason why your nose runs when you cry.
The eyelid also plays a key role. As we blink, the eyelid wipes the cornea pushing contaminants and excess fluids toward the lacrimal puncta – or the ocular surface’s drains.
If a hazardous substance is introduced into the eye, nature’s own cleansing mechanism can serve to force the contaminant into the nasal cavity, where it can be breathed into the lungs or swallowed.
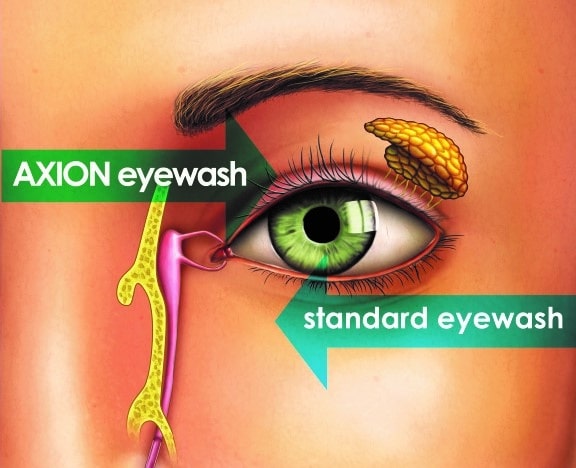
Eye irrigation: The medically consistent way
The medical profession teaches and practices irrigating eyes by introducing the flushing fluid at the inner corner of the eye – adjacent to the nose – and letting it run across the eye to the outer edge. In effect, irrigation is performed by moving the fluid away from the lacrimal puncta. This is opposite the flow direction of traditional eyewash products that flow water from the outside-in, pushing contaminants toward the inner corners of the eyes where these susceptible tear ducts, glands and canals are located. Pushing contaminants toward the nose not only risks introducing them into the nasal cavity, but also can allow the same contaminant to be introduced into the other eye.
The ideal method of irrigating eyes in any use is by using products that mirror approved medical protocols. Eyewash streams that are inverted contact the eyes at the inner canthus, or corner, adjacent to the bridge of the nose. Contaminants are thus swept away from the lacrimal system to the outside of the eye where gravity takes over and runs them into the eyewash bowl (see image). This added protection to valuable internal organs helps reduce unnecessary exacerbation of injuries.
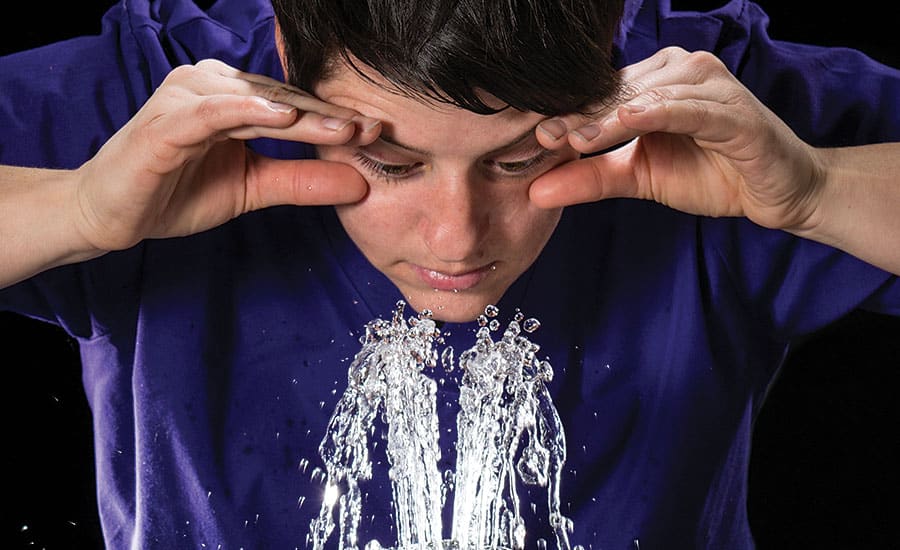
Consistent laminar flow for victim comfort
Additionally, the use of laminar flow design in the eyewash streams is another medical recommendation. A laminar flow is one in which there is an absence of turbulence, because the stream is “built” in layers. Turbulence or inconsistencies in the flow stream can strike the eye as a change in total pressure, making the victim much less comfortable during the flushing process and less likely to stay in the water for the required duration. The best approach is to provide an even, comfortable, predictable stream height and circumference, accomplished by using laminar design principles.
Times are changing, as are the protocols and practices of emergency equipment manufacturers. Irrigating eyes in a manner that is consistent with medical procedures provides the ideal situation for a victim from a comfort and effectiveness standpoint in a circumstance that may not be so ideal.
OSHA and ANSI Requirements for Eyewash and Safety Showers 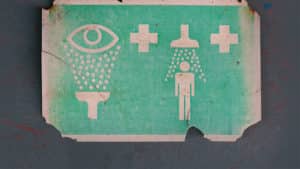
[via LabManager.com]
ANSI standard Z358.1 is detailed in terms of defining what is appropriate for safety showers and eyewash stations.
As lab managers and employees, we know that many inorganic chemicals (such as the mineral acids and alkalis) are corrosive to the skin and eyes. Likewise we are aware that many organic chemicals (such as acid halides, phenols, and so on) are corrosive and often toxic. Yet we Safety Guys are continually shocked by laissez-faire attitudes toward the use and maintenance of basic safety equipment by lab personnel, and the resultant unnecessary injuries.
One extreme example we constantly recall is the tragic UCLA accident just a few years ago, which resulted in a fatality from chemical burns.1 And we recently noticed a post on the American Industrial Hygiene Association pages for Lab Safety Chemical Exposure Incidents, where improper use of an eyewash resulted in a trip to the emergency room.2
The worker was using a fluorescent stain in the cytogenetics lab and felt something splash into his eyes. He was not wearing safety goggles or glasses. (D’oh!) Long story shortened, he flushed his eyes at the nearest eyewash, but they remained irritated and began to swell shut, necessitating a visit to the emergency room. Back at work a few days later, he noticed a coworker using the same eyewash to clean glassware and stainless steel trays, which were left resting in the sink in a cleaning solution. (What?!)
What does OSHA say?
In 29 CFR 1910.151 Medical Services and First Aid, it states that “where the eyes or body of any person may be exposed to injurious corrosive materials, suitable facilities for quick drenching or flushing of the eyes and body shall be provided within the work area for immediate emergency use.”3 OSHA doesn’t provide more specifics regarding what constitutes “suitable” or how “immediate” is defined. So how do we know if we are meeting the intent of the law?
Fortunately, we have the American National Standards Institute (ANSI), and their consensus standard Z358.1, last updated in 2014. This ANSI standard is very detailed in terms of defining what is appropriate for safety showers and eyewash stations. In fact, OSHA uses this reference as a guide when inspecting facilities. So let’s review what is “recommended” for acceptable safety equipment.
Safety shower specs
Begin by checking your facilities for the proper hardware, as recommended by Z358.1. Rest assured that OSHA will, should one or more agents show up for an inspection. For safety showers, the shower head must be capable of flowing 20 gallons per minute (gpm) at 30 psi and producing a 20-inch diameter spray pattern at 60 inches above the surface where the user stands. The center of the sprayhead pattern should be at least 16 inches from any wall, door, or obstruction. It is recommended that the shower head be mounted between 82 and 96 inches off the floor, with the valve no higher than 69 inches.
Eyewash specs
Eyewash stations target just the eyes and therefore have a lower flow requirement. ANSI Z358.1 recommends a flow of 0.4 gpm also at 30 psi. The nozzles should be at least six inches from any obstruction and mounted between 33 and 45 inches above the floor. An eyewash gauge should be used to verify and test the flow pattern.
Requirements for both
Both safety showers and eyewash stations must be able to provide the recommended flow for at least 15 minutes. This usually translates into having the equipment plumbed in with hard connections to the water supply. For example, a quick calculation for the safety shower at 20 gpm yields 300 gallons needed. Self-contained or personal wash devices are allowed, but they are considered supplemental units that can provide immediate flushing while transiting to the permanent fixture.
If the local climate presents potential for freezing conditions, the equipment must be designed to avoid freezing or protected against that situation. Activation valves must open within one second and remain open until intentionally closed or turned off. It goes without saying that these safety devices should be constructed of corrosion-resistant materials.
The 2014 update to Z358.1 added two important criteria. The first is that the requirement for tepid water is now defined as having a temperature of between 60 and 100 degrees Fahrenheit (15 to 37 degrees Celsius). The second change addresses simultaneous operation for combination units. This means that if you have a drench shower combined with an eyewash station, both devices must provide adequate flows and be fully operable at the same time.
Finally and most importantly, consider the location of equipment. We know you have the 10-second rule etched into your brain, as that is the most critical element when it comes to safety showers and eyewashes. This means that travel to the unit should be under 10 seconds for all hazardous areas that need this equipment. This equals about 55 feet. In addition, the drench shower or eyewash must be on the same level as the hazard and have a clear path for travel. We recommend painting or marking the floor area underneath the shower to help keep it clear. Z358.1 also recommends equipment be installed in a brightly lit area and marked with a highly visible safety sign.
Maintenance and training
The last thing you want is to rush to the eyewash or shower, only to be drenched with nasty, sediment-laden water. ANSI recommends flushing all equipment weekly to verify proper flow, and clearing the plumbing of any deposits. If your facility does not have floor drains installed, remember to bring a large, plastic trash can to catch the water. The weekly flushing can also provide a great training opportunity to refresh the operation and travel paths for your employees.
If you want to find out about the ANSI/ISEA Z358.1 significant requirements, attend our free 1-hour webinar on September 21st, 2017.
Register now and become subject matter experts of your emergency eyewash and shower equipment including weekly and annual testing. Request a certificate of attendance after the webinar.
This free webinar will cover:
• ANSI/ISEA Z358.1 significant requirements
• Important 2014 revision highlights
• Compliance best practices
• Live Q&A
WHAT: All You Need to Know About ANSI Z358.1 Webinar
WHEN: September 21, 2017 from 10am-11am PT / 1pm-2pm ET
PRESENTER: Justin Dunn, Product Specialist/Trainer and Samantha Hoch, Marketing Strategist
HOW: Register for free
Attendees will receive these complimentary materials after the webinar:
• OSHA white paper
• Weekly and Annual ANSI Checklist
• Access to On-Demand Webinar
REGISTER NOW>>
References
1. “tert-Butyllithium Claims Fellow Chemist at UCLA,” Chemistry Blog, January 19, 2009, http://www.chemistry-blog.com/2009/01/20/tert-butyllithium-claims-fellow-chemist-at-ucla/.
2. “Lab Safety Chemical Exposures Incidents,” American Industrial Hygiene Association, https://www.aiha.org/get-involved/VolunteerGroups/LabHSCommittee/Incident%20Pages/Lab-Safety-Chemical-Exposures-Incidents.aspx.
3. “Medical Services and First Aid,” US Department of Labor, Occupational Health and Safety Administration, https://www.osha.gov/pls/oshaweb/owadisp.show_document?p_table=STANDARDS&p_id=9806.
Haws Receives Safety 2017 Attendee Choice Award 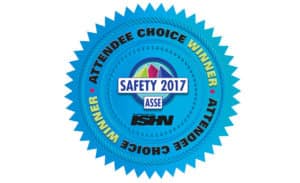
ISHN’s annual hands-on safety and health products and services awards – a complement to the Reader’s Choice Awards — are based on voting by attendees at the American Safety of Safety Engineers (ASSE) annual professional development conference.
Haws is proud to announce that our Tempered, Gravity-Fed, Portable Eyewash model 7501T is a winner in the category of Emergency Eyewashes at this year ASSE Safety 2017 conference Attendees Choice Award.
Model 7501T is a compact portable tempered eyewash and is ideal for remote locations. The 9-gallon (34 L), gravity-fed, eyewash uses a heated, insulated blanket to provide ANSI compliant tempered potable water in operating temperatures between -30° F (-34° C) and 100° F (38° C) for locations without access to a continuous potable water source. The self-contained heating blanket electrical system uses NEMA 3R rated components. 120V electrical requirement with supplied 8′ power cord.
- Featuring an FDA approved high-density green polyethylene tank easily activated by pulling the yellow activation arm down to the open position
- A wide-fill opening with threaded cap permits easy inspection, cleaning, and filling
- Relocation is simple due to the easily mounted bracket (included) and light design of this 9-gallon (34 L) portable
To see a complete line of Portable Eyewash solutions visit our website.
A Legacy of Innovation By Stephanie Kilroy
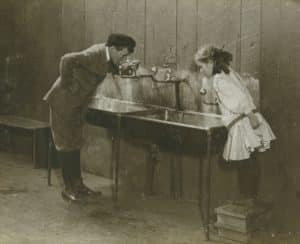
One hundred and ten years ago, Luther Haws created a drinking solution that would become the first product for Haws Sanitary Drinking Faucet Company. Luther saw children drinking from a common cup on a playground at a public school; as a result, he invented a bubblerhead drinking faucet. This innovation sparked what would eventually be an enterprise business employing over two hundred employees globally.
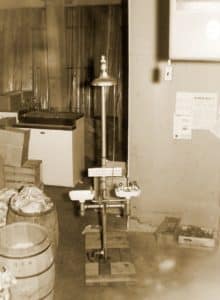
The product innovation initiated by Luther Haws continued across generations. In the 1940’s, maintenance men from an oil refinery in Richmond, CA would come by the Haws plant in Berkeley to shop for parts: round ball type bubblers, flow regulator and fittings. After inquiring about the need for these spare parts instead of completed models, Haws was informed that these parts were being used to build equipment to flush eyes. Employees at Haws sought to understand the needs of the customer and began making these emergency eyewashes and drench showers for them. This was the unofficial launch of Haws emergency equipment products; the earliest drawings date back to 1949.
Haws employees have great pride in our innovative spirit which continues to thrive in 2017. One of Haws’ recent accomplishments has been the development of a professionalized R&D department. Under the leadership of Michael Joyer, new ideas are being generated regularly with many of these innovative ideas already introduced to the market. For example, the 7501T Tempered, Gravity-Fed, Portable Eyewash was one of the first products borne out of the R&D lab.
Haws is also called to innovate, not simply with new products, but in the way we do business. We are a stable, multigenerational family company, we are learning to change and improve processes. Haws employees are looking for internal efficiencies and ways in which we can best meet the needs of our customers. Recently, the Production team has developed a cross-training initiative aimed at flexing team work assignments to serve business demands.
These types of cross-functional, support teams are increasing and delivering impactful deliverables. In Q1, Marketing and Customer Service launched a Live Chat program on the Haws website to provide immediate access to customers. The Haws China website launch is another joint effort initiative intended to widen our global marketplace coverage. Launched in Q2 2017, this was a true collaboration between the Haws China and Corporate Marketing teams. And these are just a few of the examples of all the successful small and large activities that are helping drive change to redefine how we innovate, how we grow and how we foster a culture that is rewarding for all.
One hundred and ten years later, Haws continues our commitment to inventing, designing and manufacturing hydration products as well as standardized and customized emergency response products. With more than 8,000 distribution locations and 200 employees worldwide, we continually focus on quality, service, reliability and complete solution support. Headquartered in Sparks, Nevada, USA, Haws is globally represented with locations in Switzerland, Singapore, China, India, and Brazil. For more information on Haws, visit www.Hawsco.com.
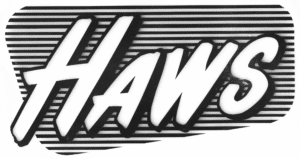
Emergency Response is a Matter of Time Written and published by: Ryan Pfund, Occupational Health & Safety Magazine
January 1, 2017
In an emergency, the faster the response, the better the outcome.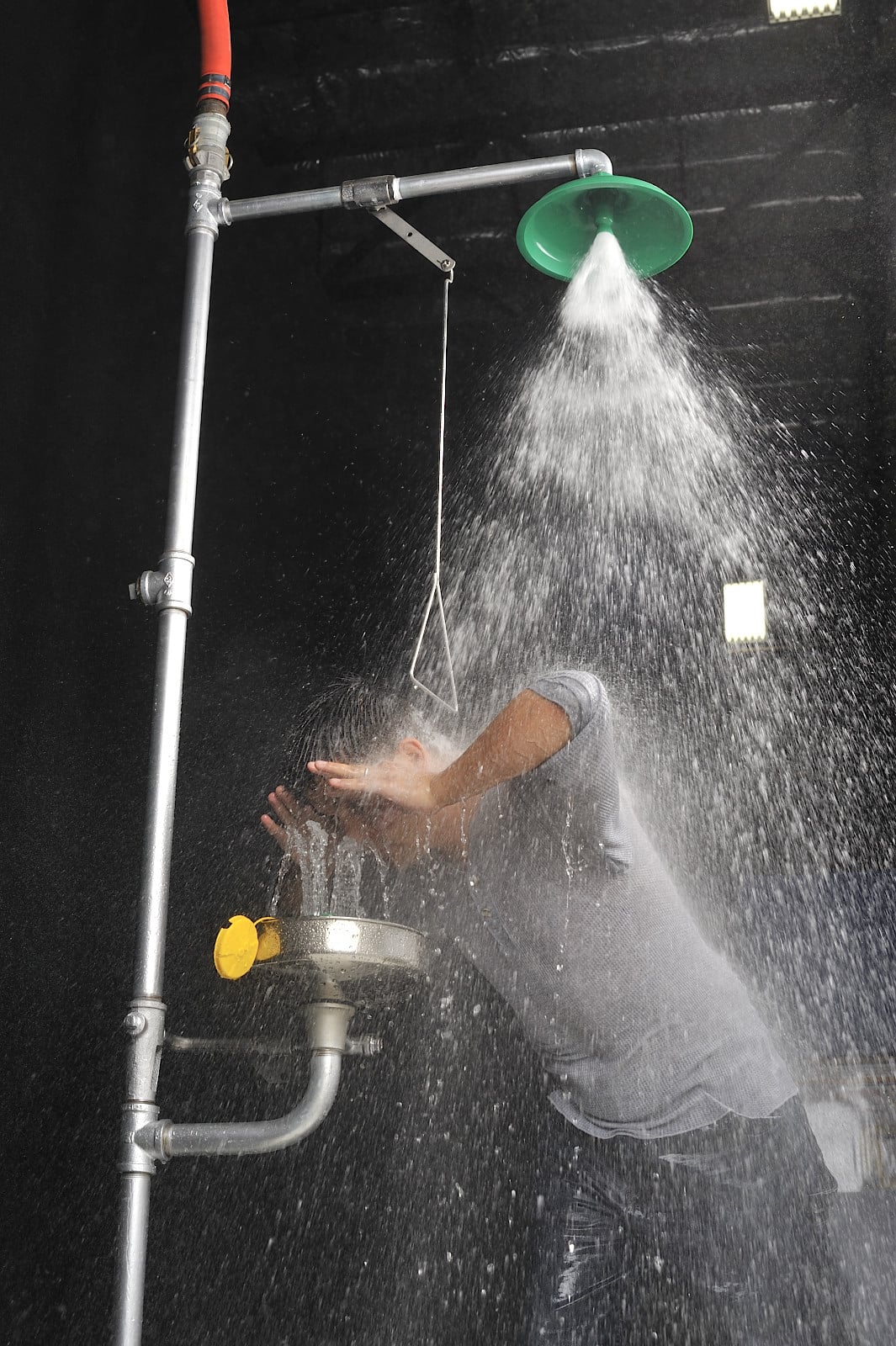
An emergency safety plan that anticipates every work site emergency and improves emergency response time is every facility manager’s and employee’s best protection. It’s difficult to think clearly and logically in a crisis, so having a well-orchestrated strategy in place that can be properly and quickly executed by employees makes all the difference.
When an employee at a work site is exposed to hazardous chemicals, taking these pre-emptive actions will help ensure the most positive outcome:
1) Providing a well-organized work site equipped with easily accessible eyewashes or drench showers
2) Minimizing the length of response time for accessing emergency equipment and drenching the employee’s affected area(s)
3) Employing emergency signaling systems to ensure immediate help is on the way, including emergency medical care
Time is clearly of the essence in stopping the exposure, alleviating discomfort and pain, and preventing further or permanent facial and bodily damage. For example, an eyewash or drench shower must be located within 10 seconds of the hazard, so the injured person can quickly and easily reach the plumbed fixture to immediately drench affected areas. Time is also a factor in the length of time one stays in the flushing fluid, which should be for a full 15 minutes as required by the ANSI/ISEA Z358.1 standard. Reaction time of emergency response personnel to swiftly gain access to the injured party is also critical in halting further injury and getting the exposed user proper medical attention.
For proper and expedient execution of a safety plan, it’s important to carefully review with employees the basics on placing and using emergency safety equipment and what to do following a co-worker’s accident. Consider these elements of emergency planning and response preparedness:
Why Use Emergency Fixtures?
Emergency safety showers and eyewashes prevent permanent eye and skin damage from chemical burns or foreign substances generated by grinding, hammering, chipping, testing, pouring, storing, transporting, and disposing operations. Proper selection, placement, and maintenance of this equipment will minimize risk of exposure while reducing the chances of catastrophic employee health impacts, work productivity, or even legal costs for the facility.
Eyewash and drench shower fixtures are placed throughout hazardous environments wherever there is risk of exposure to eye or bodily contaminants. Environments also may include inclement conditions such as heat, freezing, and airborne chemicals. Plumbed, portable, and self contained/stand-alone units should be matched to work site needs.
Where Are Proper Locations for Placement?
Each unit should be stationed close to a hazard, easily seen, and in immediate good working order. It is highly recommended to conduct a walk-through of the facility with a health or safety expert to determine proper locations and types of fixtures for each location.
Here are some fundamental placement guidelines:
- Emergency shower fixtures must be within 55 feet of a potential hazard and must take no more
than 10 seconds to access. In addition, the path to the fixture must not be obstructed by debris or other hazards that could interfere with the fixture’s use.
- The area around the fixture should be well lit to optimize visibility, and each fixture should be identified with a highly visible sign.
- If a potential chemical spill in an area is likely to affect multiple workers, a sufficient number of fixtures should be made available.
- If the worker’s ability to walk or move could be impacted by the chemical exposure, the fixture should be placed closer to the worker.
- The equipment must be on the same level on which the user is working.
When Is an Eyewash Needed vs. a Drench Shower?
After potential hazards throughout a work site are identified, consider how the types of fixtures can best address the risk:
- Emergency eyewash stations
- effective for spills, splashes, dust, or debris likely to affect only the eyes
- provides a controlled flow of water to both eyes simultaneously
- delivers an uninterrupted, 15-minute supply of tepid water; plumbed units can supply a greater volume of water available to the user—between 7.5 and 19.0 liters (2.0 and 5.0 gallons) per minute
- Emergency eye/face wash stations
- used when the entire face is at risk from spills, splashes, dust, and debris
- irrigates the eyes and face simultaneously
- provides a large distribution pattern of water (minimum 11.4 lpm/3.0 gpm) to effectively rinse the entire face
- Drench showers
- used when larger areas of the body are at risk
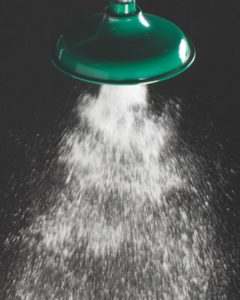
- flushes a larger portion of the body but is not appropriate for the eyes (a combination eyewash and drench shower may be used to simultaneously flush the eyes and rinse larger areas of the body)
Drench showers work by simply pulling down on the drench shower handle while standing directly underneath the shower head. New technology will effectively drench the entire body without needing to move around in the spray pattern. Eye and eye/face washes work by pushing a handle or lifting a bowl cover. The face is then positioned directly in the flushing fluid, while the user holds their eyelids open with their fingers. The user should roll his or her eyes around while positioned directly in the eyewash streams to effectively rinse the entire eye. Ensuring employees are trained on the proper and expeditious use of equipment is essential to worker safety.
For both eyewashes and drench showers, it’s essential to have direct and on-demand access to tepid water—per ANSI requirements—to encourage a full and effective flush of the affected area. ANSI Z358.1-2014 stipulates that an injured worker remains beneath the drench shower and/or flush his eyes/face for a minimum of 15 minutes to increase the likelihood of a complete and successful treatment and minimize the possibility of inadvertently spreading hazardous material to other areas.
What Is the Response Protocol After Someone Uses an Emergency Fixture?
Each employee should be trained on what action to take in assisting the affected employee(s) and how to report emergencies to emergency medical personnel. To help with the notification process, it is essential to have the ability to immediately send a clearly recognizable signal of an emergency that notifies others to help and/or send help. Using new signaling technology that works in tandem with each emergency fixture will quickly notify on-site workers and medical personnel and expedite the emergency response and recovery process.
Using a signaling system along with emergency fixtures is important because of common hindrances in the work site to alerting others. For example, industrial work environments don’t always allow for several people to be in the immediate area of a work site hazard. One person could be working outside alone or only a few people could be working within an expansive area or during third shift. These situations can affect co-workers’ capacities to be aware that an emergency is even happening and, therefore, impede their abilities to help the injured get follow-up medical care.
Another obstacle in providing immediate emergency response and post-medical care is the time it takes for emergency responders to be dispatched to a work site. According to NEDARC (the National EMSC Data Analysis Resource Center), the average emergency medical services response time in the United States is 9.4 minutes. The sooner EMS teams are alerted, the sooner they can attend to a work site emergency.
While all employees should be trained on what to do if a co-worker has been exposed to hazardous chemicals, they should not be relied upon to completely abate the emergency. It’s best to ensure proper medical response is provided in such a dynamic and emergent situation, and an emergency signaling system is a clear method to communicate when and where medical assistance is needed.
How Do Emergency Signaling Systems Work?
Signaling devices are connected to emergency showers and eyewashes. Upon activation of the fixtures, the signaling devices are automatically triggered to turn on a highly visible flashing light and a loud sound designed to cut through ambient noise. The signaling systems call others to help, draw attention to the precise location of need, alert management to contact first responders, and provide remote monitoring of safety equipment.
Installing an emergency signaling system is a much faster and efficient way to alert those in the immediate area, as well as managers or safety personnel in other locations, that an employee is in need of help. It’s important to make sure various alarms in the facility are highly distinctive and recognized by all employees as a signal to response actions identified in your plan.
The first seconds following eye and skin exposure are absolutely critical to minimizing worker injury, which is always the main goal of any worker safety program. Instituting a well-devised safety plan, having access to proper emergency equipment, and providing a reliable emergency signaling system can expedite response and improve the outcome of the emergency.
Access is everything: Eyewash stations & showers must be ready when needed Repost from ISHN
Written by Sally Smart
Sally J. Smart is a Technical Safety Specialist for Grainger. She is a Board Certified Safety Professional® (CSP) and a Qualified Safety Sales Professional (QSSP). Sally is OSHA – 30-hour trained for both Construction and General Industry and is an OSHA Authorized Outreach Trainer for General Industry.
When working with corrosives, drenching facilities should be readily available. According to OSHA’s Medical and First Aid Standard 29 Code of Federal Regulations (CFR) 1910.151(c) “Where the eyes or body of any person may be exposed to injurious corrosive materials, suitable facilities for quick drenching or flushing of the eyes and body shall be provided within the work area for immediate emergency use.” These drenching facilities could include an eyewash, eye/face wash, shower or combination eye/face wash shower depending on the amount of possible exposure.
Since OSHA does not clarify what the minimum requirements for “suitable facilities” are, employers look to the voluntary American National Standards Institute (ANSI) Z358.1-2014 Standard for Emergency Eyewashes and Shower Equipment for guidance. ANSI Z358.1-2014 helps users select and install proper emergency equipment to meet OSHA requirements. Also, OSHA often uses ANSI Z358.1 as a guide during inspections and may elect to issue penalties for those found not to be in compliance.
ANSI Z358.1-2014 Requirements
To ensure that eyewash stations and showers are always ready when needed, it is important that the requirements for test procedures and maintenance set forth in Z358.1-2014 be followed.
ANSI Z358.1-2014 is divided into five sections and each section addresses how the equipment should perform, as well as testing procedures for ensuring proper operation, installation, maintenance and training.
The requirements for testing and maintaining eye, eye/face washes and showers are based on the manufacturer’s instructions and ANSI protocols. Generally, the manufacturer’s instructions state that the units should be inspected and tested and the results recorded weekly. Individual owner manuals should be reviewed for the specific manufacturer’s guidelines.
Plumbed and Self-Contained Emergency Showers, Eyewash Equipment, Eye/Face Wash Equipment and Combination Units Performance and Maintenance Criteria:
- Valve should easily activate in a second or less and remain open on its own until it is intentionally turned off
- If a potential for freezing exists, product specifically designed to avoid freezing should be used
- Plumbed units should be activated on a weekly basis long enough to ensure that flushing fluid is provided
- • Plumbed and self-contained showers must maintain a minimum flushing fluid of 20 gallons per minute (GPM) at 30 pounds per square inch (PSI) for 15 minutes
- Plumbed and Self-Contained Eyewash Equipment must maintain a minimum flushing fluid of 0.4 GPM at 30 psi for 15 minutes
- Eye/Face wash equipment must maintain a minimum flushing fluid of 3 GPM at 30 PSI for 15 minutes
- Determine that flushing fluid is tepid (between 60 – 100°F)
- Determine that flushing fluid is dispersed throughout the required pattern
- Showers, eyewashes, eye/face washes, and drench hoses all can be utilized in combination units and the requirements of each of these types of product categories must be met when utilized with other categories of emergency equipment
- Self-contained units should be visually inspected and needed fluid replacement determined
Supplemental Equipment
- Supplemental equipment is intended for immediate use and must be followed up by the usage of emergency product that can provide a minimum of 15 minutes of flushing fluid continuously
- Personal eyewash units and drench hoses are considered supplemental equipment
Annual inspections
Each year emergency products must be inspected to ensure they comply per the ANSI standard. While a fixture may be certified to meet the ANSI standard, once installed, it is important to make sure it is installed according to the standard’s requirements.
Weekly checklist
- Initial and date in the corresponding box verifying that the emergency eyewash/shower is checked weekly to ensure:
- Equipment is installed within 10 seconds from the hazard and on the same plane as the hazard
- Pathway is clear of obstructions
- Equipment is activated to ensure compliant operation and to clear any sediment
- Equipment is free of broken or missing parts
- Equipment is protected against freezing
- User is protected from scalding water
Save critical seconds
Always inspect and test emergency eyewashes and showers if there is any doubt about their dependability. Identify problems or concerns and establish a regular maintenance program. Consult the manufacturers’ operating manual and ANSI Z358.1-2014 for guidance on test procedures, maintenance, operation and training.
Inspection, testing and maintenance of the emergency eyewash/shower equipment helps ensure that it will function properly when needed. Studies show that the seconds immediately following an eye or body injury caused by a corrosive are often critical to minimize damage.
HAWS EMERGENCY SHOWER AND EYEWASH SITE SURVEY PROGRAM
As the industry leader, Haws can help bring awareness to the hidden dangers of inadequate emergency response by providing your facility the opportunity to receive a complimentary ANSI compliance emergency shower and eye/face wash survey. The onsite review includes a detailed inspection report, executive summary chart, summary of recommendations, and an interactive debriefing to review material.
By taking advantage of Haws’ ANSI Emergency Shower and Eye/Face Wash Survey Program, you will be able to ensure your facility not only meets the most recent ANSI Z358.1 Standards, but also provide proper functionality and appropriate first aid capabilities in the event of an emergency.
Learn more about the Haws Survey Program.
Eyewashes: Is It “1 Second” or “1 Motion”? DOWNLOAD THIS FLYER
The ANSI Z358.1 Standard (American National Standard) mandates that proper eyewash activation – which describes a unit going from “off” to “on”- shall take one second or less. This requirement has held true since the inception of the ANSI Standard in 1981 and throughout all revisions including 1990, 1998, 2004, 2009 and 2014. Despite this, the myth that the eyewash must go from “off” to “on” in one motion continues to be inaccurately shared.
To quote the 2014 Standard: “The valve shall be simple to operate and shall go from “off” to “on” in 1 second or less.”
This disconnect in awareness of the activation requirement has come up especially pertaining to faucet-mounted eyewashes where it is required for the user to turn on the water supply and then activate the unit, hence a two motion activation.
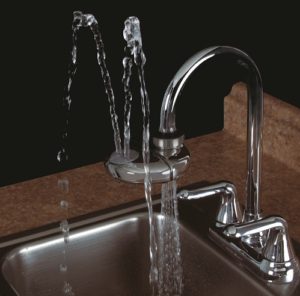
Specifically, the Haws® AXION® eyePOD® faucet-mounted eyewash has proven through testing that it meets the “off to on in one second or less” activation requirement.
Mounting easily to standard faucets, the AXION eyePOD provides healthcare offices, laboratories, schools, and even households with medically consistent inverted eyewash flushing technology.
As seen below, a simple rotation of the unit transforms normal faucet capabilities into a fully-functioning, ANSI compliant eyewash station.
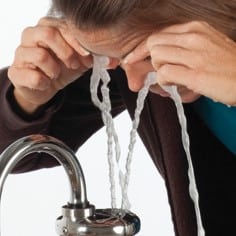
Medically Superior Response®
The trademarked inverted water streams gently flush contaminants away from sensitive glands and ducts that surround the eye. The added protection to these valuable organs helps reduce against unnecessary injury.
DOWNLOAD THIS FLYER
Click here to learn more about the AXION eyePOD.
If interested in pricing information or receiving a quote, click here.
For more information on the ANSI Z358.1 Standard for emergency showers and eyewashes, visit our ANSI Resources page.
ANSI Z358.1 DEBATE: “1-Touch” vs. “1-Second” Activation The ANSI Z358.1 Standard (American National Standard) mandates that proper eyewash activation – which describes a unit going from “off” to “on”- shall take one second or less. This requirement has held true since the inception of the ANSI Standard in 1981 and throughout all revisions including 1990, 1998, 2004, 2009 and 2014. Despite this, the myth that the eyewash must go from “off” to “on” in one motion continues to be inaccurately shared.
To quote the 2014 Standard: “The valve shall be simple to operate and shall go from “off” to “on” in 1 second or less.”
This disconnect in awareness of the activation requirement has come up especially pertaining to faucet-mounted eyewashes where it is required for the user to turn on the water supply and then activate the unit, hence a two motion activation.
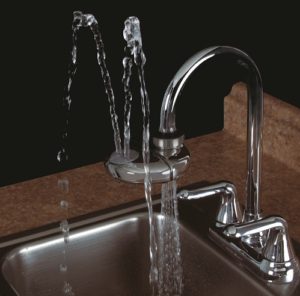
Specifically, the Haws® AXION® eyePOD® faucet-mounted eyewash has proven through testing that it meets the “off to on in one second or less” activation requirement.
Mounting easily to standard faucets, the AXION eyePOD provides healthcare offices, laboratories, schools, and even households with medically consistent inverted eyewash flushing technology.
As seen below, a simple rotation of the unit transforms normal faucet capabilities into a fully-functioning, ANSI compliant eyewash station.
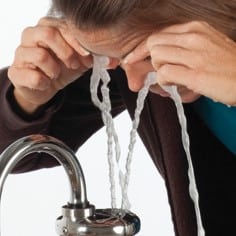
Medically Superior Response®
The trademarked inverted water streams gently flush contaminants away from sensitive glands and ducts that surround the eye. The added protection to these valuable organs helps reduce against unnecessary injury.
Click here to learn more about the AXION eyePOD.
If interested in pricing information or receiving a quote, click here.
For more information on the ANSI Z358.1 Standard for emergency showers and eyewashes, visit our ANSI Resources page.
The Difference Between AXION and Other Eyewashes AXION® is an eye/face wash that covers not only the eyes but the entire face unlike most other products that just flush the eyes. Secondly, the AXION inverted water streams protect sensitive eye ducts and glands.
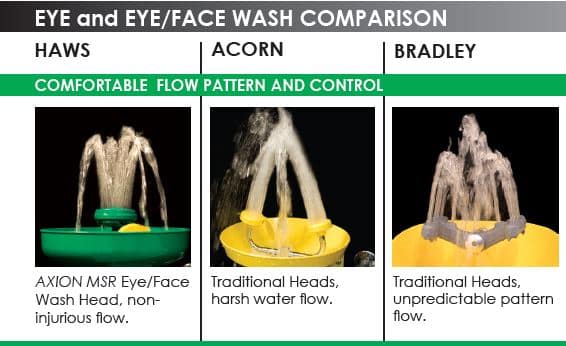
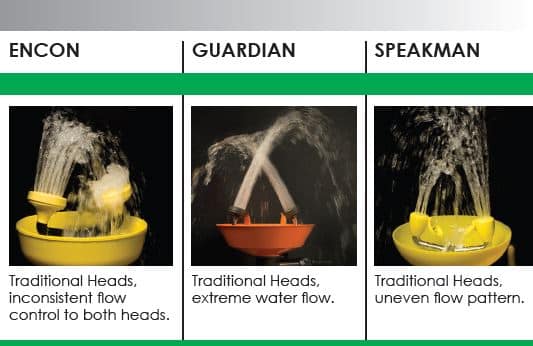
Additional features:
• Smooth laminar flow provide comfortable water pressure
• ANSI Z358.1 compliance for velocity, stream height, and gallons per minute
• Predictable stream height provides enhanced victim comfort for full 15-minute flush
• In-line strainer collects debris to help reduce injury aggravation
• Stainless steel ball and valve for durability
• Pre-built and fully water tested for reliability
• Integral flow control designed to match flow needs for ANSI compliance
• Customized facility options with corrosion-resistant ABS plastic or stainless steel
To learn more about the AXION technology, click here>>
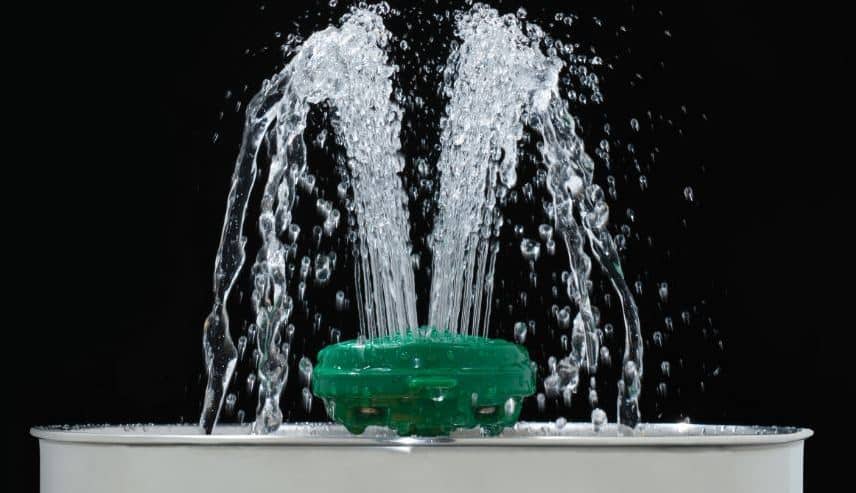
Ready to retrofit your existing eyewashes to the AXION Technology? Our AXION Advantage® kits do just
that. The kits are supplied with adapters to convert 80% of competitive units including Acorn®, Bradley®, Encon®, Guardian®, and Speakman®. Simply twist off the old eyewash heads, apply the correct adapter, twist on the AXION eye/face wash head, and test for ANSI compliance! Click here to learn more or buy now!
REPOST: Workplace Eye Wellness Month
KEEPING AN EYE ON CUSTODIAL WORKER SAFETY
Contributed by BSN Staff
Wednesday, March 2, 2016
CHARLOTTE, NC — Because March is Workplace Eye Wellness Month, the National Service Alliance, a leading group purchasing organization for the professional cleaning industry, is releasing the following suggestions for contract cleaners and custodial workers to help them protect their vision.
Custodial workers rank “above average” when it comes to job-related injuries, according to the U.S. Department of Labor, and this includes eye injuries.
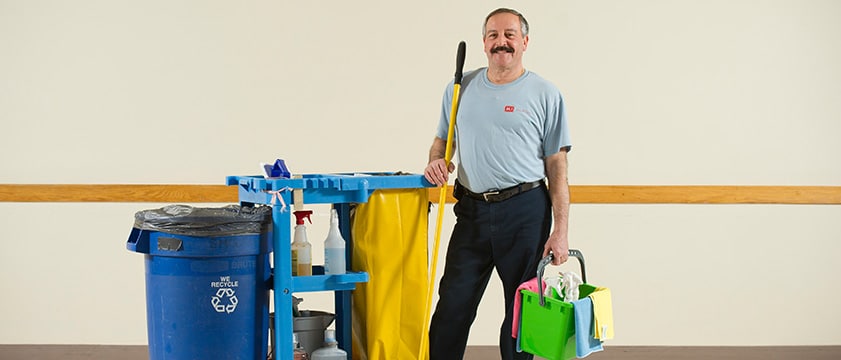
“While a chemical splash can burn the eye, causing one of the most serious forms of eye injuries, it certainly is not the only type of hazard impacting the eyes of custodial workers,” says Tobi Colbert, business development manager at the NSA. “Very often eye injuries are the result of small airborne particles or objects striking the eye, such as metal slivers, dust, even staples and nails.”
Because of this Colbert says custodial workers should wear eye protection at all times. Among her other suggestions are the following:
*All cleaning contractors should install an emergency eye-drenching and flushing center in the facilities they maintain.
* The emergency eye care center should be easily accessible and take no more than 10 seconds to reach.
* Workers should try on different goggles to test for comfort. Goggles should fit comfortably, stay in place, and have side protection.
* If more protection is needed, especially when working with chemicals, a face shield should be worn over the goggles.
* Workers should wear goggles with “indirect” venting to protect from chemical splashes.**
* Select eye gear with an anti-fog coating. “If the goggles fog up, the worker may take them off and forget to put them back on. This becomes an accident just waiting to happen.”
“Cleaning contractors should also know there are ANSI standards for protective eye gear,” adds Colbert. “They have been tested and certified to help protect worker’s eyes.”
The NSA is a buying group serving the professional contract cleaning industry.
via [Building Services Management]
|