Webinar Invitation:
YOUR GUIDE TO CHOOSING
THE PROPER EMERGENCY EQUIPMENT
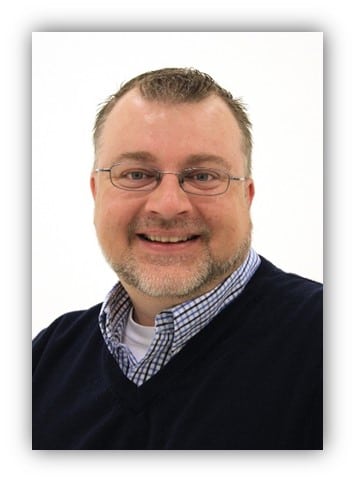
Canadian Center for Occupational Health and Safety (CCOHS) on Emergency Showers and Eyewashes
HOW DO I KNOW IF I NEED A PORTABLE OR PLUMBED EMERGENCY SHOWER/EYEWASH PRODUCT?
The most costly injury of the more than 5 million unintentional work related injuries in the US involves the head, averaging $82,382 per claim. In any environment, occupational safety should be taken very seriously and appropriate emergency response is a crucial component to the overall safety of your employees and your company.
The Occupational Safety & Health Administration (OSHA), 29 CFR 1910.151, requires that “Where the eyes or body of any person may be exposed to injurious corrosive materials, suitable facilities for quick drenching or flushing of the eyes and body shall be provided within the work area for immediate emergency use.” OSHA turns to The American National Standards Institute (ANSI) Z358.1-2014 Standard for specifics on selection, installation, operation and maintenance requirements.
Proper emergency equipment selection is a function of knowing your risks, the characteristics of the materials you work with, and logical consideration of the variety of products and design configurations available.
Once you’ve determined that an emergency station is needed, you need to define whether a portable or plumbed station is most appropriate. But first, you must be aware of the difference. A portable eyewash is a self-contained ANSI-compliant emergency response product that is needed for locations without access to water and can be moved at a moment’s notice to meet the rapidly evolving needs of a chemical, manufacturing, or construction environment. There are various types of portable eyewashes including gravity-fed, air-pressurized, and personal squeeze bottles (reference ANSI Z358.1 Supplemental Equipment/Personal Wash Units (Section 8.1)). Portable stations can provide added flexibility that is a benefit in to
day’s dynamic work settings. A plumbed unit is just as it sounds; a permanent emergency response solution that is in a fixed location connected to a continuous source of potable water with sufficient flow and pressure for ANSI compliance and victim comfort.
ANSI Z358.1 requires that all emergency stations, portable or plumbed, must provide sufficient flow (flow rate depends on product type i.e. eyewash vs. eye/face wash vs. shower) for a minimum of 15 minutes. They are also required to be located within 10 seconds of the potential hazard. Supplemental eyewashes, such as personal squeeze bottles, are a useful solution while a victim is en route to primary equipment.
In addition to water source, ask yourself these questions when determining if a portable or plumbed unit is needed:
- Does the potential hazard stay in the same location within the facility or is it mobile? If it is static work station, a plumbed unit is the recommended product choice and must be installed within 10 seconds of the hazard. If the hazard is mobile such as a construction site, a portable product is recommended and is to be placed within 10 seconds of the hazard.
- Does the location need tempered water (60-100°F/16-38°C)? If the emergency fixture will be located in areas where the internal water temperature could drop below 60°F (16°C) or rise above 100°F (38°C), the water temperature will need to be regulated. Most portable units do not provide an option for tempered water, therefore a plumbed unit along with a tempering solution is the recommendation. Although, a few manufacturers do offer a tempered portable station.
Maintenance of portable and plumbed units differ. As portable units hold stagnant water, they are required to be drained and refilled with potable water on a more frequent basis. Most eyewash manufacturers offer a sterile preservative that keeps the water for an average of 3 months. On a weekly basis, ANSI requires a visual inspection should take place to ensure unit is full and clean. Regarding plumbed units, there is an ANSI-mandated weekly activation requirement to verify proper operation and to flush buildup that may have formed due to stagnant water in the piping and unit.
It’s impossible to predict when an injury will harm a workers’ eyes, face or body, but it is possible to take proactive preventative measures by supplying the appropriate emergency response equipment for maximum victim comfort and response.
To download or print this white paper, click here.
Infographic: Top 3 Usage Locations of Portable Eyewashes
What are portable eyewash stations?
A portable emergency eyewash is a self-contained ANSI Z358.1 compliant emergency response product that is needed for locations without access to water and can be moved at a moments notice to meet the rapidly evolving needs of a chemical, manufacturing, or construction environment.
When is a portable eyewash station needed?
A portable emergency eyewash can be used anywhere an emergency eyewash system is needed but does not have access to a continuous source of potable water. The advantage over plumbed units is the mobility feature. This allows safety professionals to relocate the equipment as needed to stay compliant with ANSI and OSHA emergency equipment distance requirements.
Free Site Inspection of Your EquipmentHave emergency showers and eyewashes in your facility? Do you know if they are compliant with the most recent ISEA/ANSI Z358.1- 2014 Standard? Don’t stress, we’ve got your back.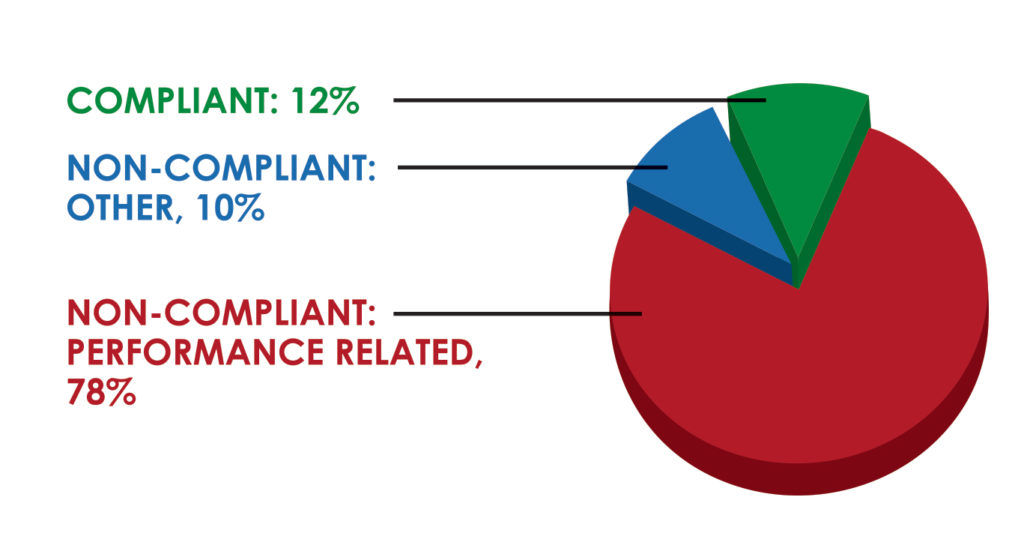
We are offering you a COMPLIMENTARY full day site inspection of you existing emergency response equipment, regardless of brand. And that’s not even the best part…
Once the physical equipment inspection is completed, we’ll provide you a full detailed report which will include the status of each piece of equipment, an executive summary, and…
A full recommendation report detailing what we recommend you need to do to upgrade your equipment to ensure ANSI compliance!
As if that’s not enough, all you have to do to take advantage of this offering is fill out a form! Then, a Haws Representative in your area will reach out to you to schedule the site visit.
Now, how in the world to you pass up an opportunity like this?? You just don’t. So go ahead and hit the pretty green button below to get started!
[button link=”https://www.hawsco.com/support/survey/” style=”tick” color=”green” bg_color=”#009b39″] SIGN UP NOW[/button]
Preparation: The Best Guard to an EmergencyDo you know the protocol to flushing hazardous chemicals off of your body in an emergency? It’s always a good rule of thumb to be knowledgeable on how to properly execute safety shower and eyewash performance in an emergency situation. Take the time to get to know the mechanics of the emergency equipment in your facility before an accident takes place. Casey Hayes, director of Haws Integrated™, recommends the following:
- Get a proper training session on emergency equipment. Be aware of the location of the unit and how long it takes to arrive at the unit from your work space.
- Confirm that it should not take more than 10 seconds to arrive to the emergency equipment.
- Upon arrival to the shower, pull lever and remain in shower for a full 15 minutes. This is to ensure the prevention of chemical absorption while it also helps to cool burns and prevent hypothermia.
- When using an eyewash or eye/face wash, hold eyes open during the entire 15 minute flushing period.
- In some cases, it may be appropriate to have a partner with you during the state of emergency. If you work alone, you may not have the opportunity to have someone assist you. We recommend that if you are in a state of shock, have a co-worker assist you to the emergency shower and or eyewash station. If you are saturated in chemicals, it is best not to expose anyone else and to proceed to the emergency station alone.
- Always go to the emergency room following the use of the emergency shower and/or eyewash.
Furthermore, it’s essential to have functional emergency showers and eyewashes throughout your facility. Refer to our previous blog post ANSI Z358.1 FAQ: What is the Weekly vs. Annual Test for a break down on when it is appropriate to perform each test. We also offer a free webinar on the requirements for emergency eyewashes and showers. Click here to watch.
ANSI Z358.1 FAQ: What is the Weekly Test vs. the Annual Test?
Are you unsure of when you should test the emergency showers and eyewashes in your facility? Do you know the difference between the weekly and annual testing requirements? In certain cases, a full 15-minute drench period is not required, however it is important to know what is required on a weekly basis versus annually.
ACTIVATE WEEKLY
Per the ANSI Z358.1 standard, you are required to activate the emergency equipment weekly to verify operation and to ensure there is a flushing fluid supply and clear the supply line of any sediment build-up that could prevent the flushing fluid from being delivered due to stagnant water.
How long do you activate for? ANSI states the duration of the weekly activation depends on the amount of water contained in the unit itself and all sections of pipework that are not a part of a constant circulation system, also known as the “dead leg” portions. The goal of the weekly activation is to flush out the stagnant water in the dead leg completely.
TEST ANNUALLY
All emergency eyewashes, eye/face washes, showers and combination units are required to be fully inspected annually to ensure conformance with the installation section of the Z358.1 standard for that type of equipment. The following some of the requirements that need to be met for the annual test:
- The equipment must be assembled and installed in accordance with the manufacturer’s instructions, including flushing fluid delivery requirement.
- Equipment must be accessible within 10 seconds, located on the same level as the potential hazard, and must be free of obstructions that may inhibit immediate use.
- Must be identified with well-lit, highly visible signage.
- Equipment must be connected to a supply of flushing fluid that can produce the required flush time of a full 15 minutes.
- Where the possibility of freezing conditions exists, equipment must be protected from freezing or freeze-protected equipment must be installed.
- Must deliver tepid flushing fluid for the full 15-minute drench period.
- Equipment must go from “off” to “one” in one second or less.
- Must provide a controlled flow of flushing fluid at a velocity low enough to be non-injurious to the user.
How long do you activate for? As stated above, you need to ensure the equipment is is delivering tepid flushing fluid for a full 15 minutes.
For full detailed information on the ANSI Z358.1 requirements for Emergency Eyewashes and Showers, watch the FREE on-demand webinar HERE.
For more ANSI resources such as a testing checklist, click here.
How To Protect Your Workers From HypothermiaEMERGENCY RESPONSE BEST PRACTICES :: PROTECTION AGAINST HYPOTHERMIA
Low ambient temperature and wind chill may simply be part of the job in cold climates, but they can have a lethal effect on exposed skin – particularly when combined with hazardous conditions where safety showers are required. This problematic combination creates a scenario for an ineffective and injurious emergency shower response. In some cases, inappropriate safety equipment can actually speed up the potential for cold-temperature related injuries like hypothermia. To ensure everyone’s safety, awareness and adherence to proper procedures and safety standards is critical.
UNDERSTANDING COLD-TEMP RELATED INJURY RISKS
Occupational Safety & Health Administration (OSHA) defines hypothermia as a cold-temp related injury in which normal body temperature drops to or below 95°F/35°C. Symptoms include drowsiness or fatigue, bluish skin, uncontrollable shivering, slurred speech and clumsy movements. Permanent tissue damage and death can result if hypothermia is left untreated.
EXPOSED FLESH in 0°F/17.8°C with 10mph wind
speed is in danger of hypothermia within 1-minute
Specific conditions in cold-weather climates can increase the risk of cold-temp related injuries, including hypothermia, which can affect a person even when land temperatures are above freezing or water temperatures are below 98.6oF/37oC. Factors influencing these injuries include:
• Low ambient temperatures and/or wind chill
• Wet skin, which freezes at a higher temperature than dry skin
• Exposed skin
While the ANSI Z358.1 Standard outlines suitable water temperatures as tepid – with a defined range of 60 to 100°F/15.5 to 37.77°C – and requires a full 15-minute drench period, the low end of this accepted temperature range can exacerbate the effects of hypothermia, particularly when exposure lasts the entire drench period. In addition, ANSI Z358.1 Appendix B6 states: Colder ambient temperatures might require an enclosure for added protection – even with water supplied in the ANSI Z358.1 specified temperature range, there is a high risk of hypothermia for wet victims exposed
to frigid ambient temperatures where loss of body heat is intensified by the effects of evaporative cooling and wind chill. It is crucial that the proper safety shower system is provided to prevent an incident where hypothermia could intensify an injury to a victim already in a hazardous situation.
SAFETY SOLUTIONS FOR COLD-WEATHER CLIMATES
Haws Integrated™ offers a variety of customized, ANSI compliant enclosed safety solutions for all climates. Features specific to equipment intended for use in cold-weather climates include combination units enclosed in booths with all-weather insulation, water-proof exterior coating, self-closing shower doors, built-in heaters, internal hot water supply and medically superior, non-injurious water flow, all of which qualify as industry best practices. Enclosures eliminate frigid environments by providing a shower area at a safe ambient temperature, out of the elements. Properly preparing a site for the use of climate specific equipment can mean the difference in minimizing or increasing the severe effects of cold-temperature injuries.
For more information, visit HawsIntegrated.com.
These 5 Emergency Equipment FAQ’s Can Keep You Out of Trouble1. How do you determine if you need a safety shower versus just an eye/face wash?
It depends on what the potential hazard is. We advocate that an eye/face wash should be the requirement over an eyewash as it is rare for a chemical to only splash into your eyes and not on your face as well. A combination shower and eye/face wash is necessary when the SDS for the chemicals you are using require one. If contact with the skin is not harmful, but contact with eyes would be, then an eyewash or eye/face wash only is suitable. If there is any potential hazardous skin contact, then a shower is most appropriate.
2. What are the types of chemicals when used in the workplace require the use of an eyewash station?
We recommend viewing your SDS’s (safety data sheet) and looking under the Proper PPE and First Aid requirements. Most SDS’S require some sort of emergency equipment along with a required flow time of 15 minutes and sometimes longer.
3. For portable or gravity-fed eyewash stations, what’s the standard for draining and refilling the tank? Along with the additive.
As there are a couple of different designs on the market, I cannot provide a specific “standard” you should follow. The ANSI requirement is that any portable or self-contained eyewash should be visually inspected weekly to determine if the flushing fluid needs to be exchanged or supplemented. The units should be maintained as per the manufacturer’s specific model instructions. For Haws, and most other manufacturer’s units, using potable water and a sterile bacteriostatic additive exchange is required every three months as well as rinsing the unit clean between the exchanges. If you are not using an additive, then the water should be exchanged on a minimal weekly basis, with a thorough tank cleaning monthly.
4. What is the standard for testing the eyewashes and showers?
ANSI Z358.1 has specific standards for testing based on the type or style of equipment in use. As a general statement, equipment needs to be inspected weekly to ensure that there is a flushing fluid supply and that the equipment is in good repair. If the equipment is of a plumbed design, then it should also be activated weekly to clear the supply line of any sediment build up and to minimize any microbial contamination due to stagnant water. The weekly inspection also looks at the location to ensure that the equipment is well lit, identified with signage, free of obstruction and on the same level as the hazard. Annually, the equipment needs to be inspected against all aspects of the ANSI Z358.1 standard including flow capabilities, temperature and irrigation patterns. Please view our full on-demand ANSI Standard web seminar on our Haws YouTube page.
5. What requirements are there for disposing used water from an eyewash or shower?
Waste or “grey” water is not in the scope of the ANSI Z358.1 standard however the appendix of the standard does call out that consideration should be given to proper disposal of waste flushing fluids. Freezing temperatures, drainage, elevated showers, and pollutants are some but not all of the considerations. It may depend on your specific situation so I would recommend consulting authorities on your local, state, and federal regulations.
REPOST: Trends in Emergency Eyewashes/ShowersRepost from Safety & Health article by Tracy Haas
Equipment reliability is imperative
Unlike personal protective equipment such as hard hats and steel-toe boots, emergency eyewashes and showers are not meant to be used every day. Ideally, a worker will never need one. But should an incident such as a chemical splash occur, it’s vital that emergency eyewashes and showers be ready for use.
Issues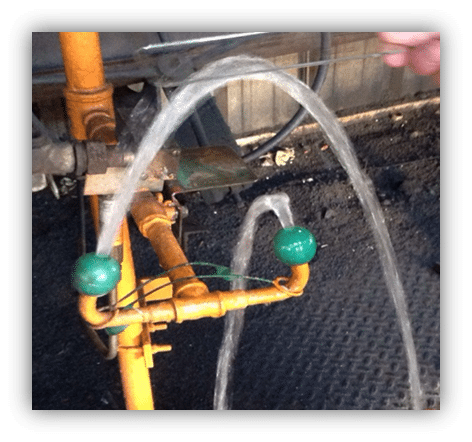
Because emergency eyewashes and showers are not frequently used, their maintenance may not always be top of mind. “The two most common emergency shower misuses are not providing ANSI-required tepid water and failing to conduct weekly test activations to ensure the units are working,” said Ryan Pfund, senior product manager, emergency fixtures, for Menomonee Falls, WI-based Bradley Corp. Pfund recommends establishing a weekly inspection program to test your company’s eyewash and shower equipment to ensure it is working properly and providing tepid water instantaneously. “Manufacturers provide specially designed devices and materials to assist in testing,” he added.
Nuray Ebel, product manager at Sparks, NV-based Haws, echoed Pfund’s comment that ANSI Z358.1-required weekly testing – although crucial – is often neglected: “The most significant part of the weekly test is the validation that the equipment provides proper first aid to users – not just ensuring water is present.”
Keith Flamich, marketing manager for Chicago-based Guardian Equipment, notes that equipment reliability is imperative. “During incidents where emergency eyewash and shower units are activated, far too much is at stake to depend on equipment that is not properly tested and not third-party certified,” Flamich said.
What’s new
Emergency eyewashes and showers now have improved flow control and coverage, according to Pfund. “The newest models apply fluid dynamics technology that works with a pressure-regulated flow control to provide an integral and uniform flow of water directed at the affected area,” he said.
Flamich pointed to the increasing popularity of heat-traced freeze-resistant stations in cold-weather environments. “These units are manufactured with a heat-tracing cable wrapped around internal piping to prevent the freezing of standing water within the unit,” he said. “Once activated, a safety station first delivers the standing water before drawing from a tepid water supply.” However, he cautioned that these stations are commonly misunderstood, and people often believe the units are capable of heating a full 15-minute supply of water per the ANSI Z358.1 tepid water requirement. “The reality is that these units heat only the standing water contained within its internal piping prior to unit activation,” Flamich explained. “As such, there must be continuous source of tepid water supplying the heat-traced safety station (i.e., thermostatic mixing valve, tepid water loop, or instantaneous water heater) to meet the ANSI-required 15-minute tepid water flush.”
On a separate note, Ebel spoke of the benefits of using wireless alarm technology for emergency eyewashes and showers. “Wireless transmitters enable control and/or notification from remote areas where wiring or wire maintenance is not physically possible or economically feasible.”
Increase In OSHA Fines Now in EffectFor the first time in twenty-five years, OSHA penalties are increasing – and significantly. A federal act passed in 1990 exempted OSHA from increasing fines to account for inflation, but the new budget signed into law on November 2, 2015, includes an amendment striking that exemption.¹
The “Catch-Up Adjustment,” based on the percentage difference between October 1990 and the Consumer Price Index Budget of October 2015, will amount to a penalty increase of about 80%. That will bump the current $7,000 cap on serious OSHA violations to about $12,500, and the willful, repeat violations penalty of $70,000 to just over $126,000. Once this one-time adjustment is made, OSHA will also be required to adjust penalties annually using the Consumer Price Index’s yearly percentage increase.²
Budget changes will go into effect on July 1 of 2016, and increased penalties will begin August 1 in all states regulated by OSHA. For employers, now is the time to ensure that workplace safety programs and equipment are meeting appropriate standards. This includes:
• Confirming that employee safety training is comprehensive and documented
• Assessing workplaces for potential hazards and addressing them in the most appropriate manner
• Addressing employee safety concerns
• Confirming that existing safety equipment is fully compliant and operational
Consider the OSHA penalty hike a boon for workplace safety. Studies have shown that workplace injuries are reduced in settings in which health and safety inspections have direct consequences for violations.³ And while it can be asking the impossible to build a system with the resources to inspect every single workplace for violations, increasing employer awareness about steep financial penalties for non-compliance may well do the trick. An 80% increase in current OSHA fines will likely prove an effective method of stressing the importance of workplace safety.
Interested in learning if your facility is ANSI compliant? Sign up for a complimentary, one-day onsite ANSI Survey at www.Hawsco.com/survey.
TO DOWNLOAD THIS WHITE PAPER, CLICK HERE.
¹OSHA fines to increase significantly. (2015, November 5) Retrieved from http://www.safetyandhealthmagazine.com/articles/13258-osha-fines-to-increase-significantly
²Employers beware: OSHA fines are on the rise for the first time in twenty-five years. (2015, November 11). Retrieved from http://www.oshalawupdate.com/2015/11/11/employers-beware-osha-fines-are-on-the-rise-for-the-first-time-in-twenty-five-years/
ÂłInspections with penalties linked to lower injuries: IWH review. (n.d.)Â Retrieved from http://www.iwh.on.ca/at-work/81/inspections-with-penalties-linked-to-lower-injuries-iwh-review
Pulp and Paper Mill Upgrades it’s Emergency EquipmentOne of the leading manufacturers of corrugated and consumer packaging in North America is committed to exceeding expectations for both its customers and its more than 15,000 employees throughout all facets of the organization.
When a new site safety manager joined the organization, he suspected there were issues with the plant’s emergency response equipment, particularly safety showers and eyewashes.
Following a thorough review of Haws safety shower and eyewash survey results, the safety manager purchased 40 AXION Advantage™ kits to retrofit the majority of the plant’s existing showers and eyewashes, which included product from a variety of companies.
To read the full case study, click here>>