Have emergency showers and eyewashes in your facility? Do you know if they are compliant with the most recent ISEA/ANSI Z358.1- 2014 Standard?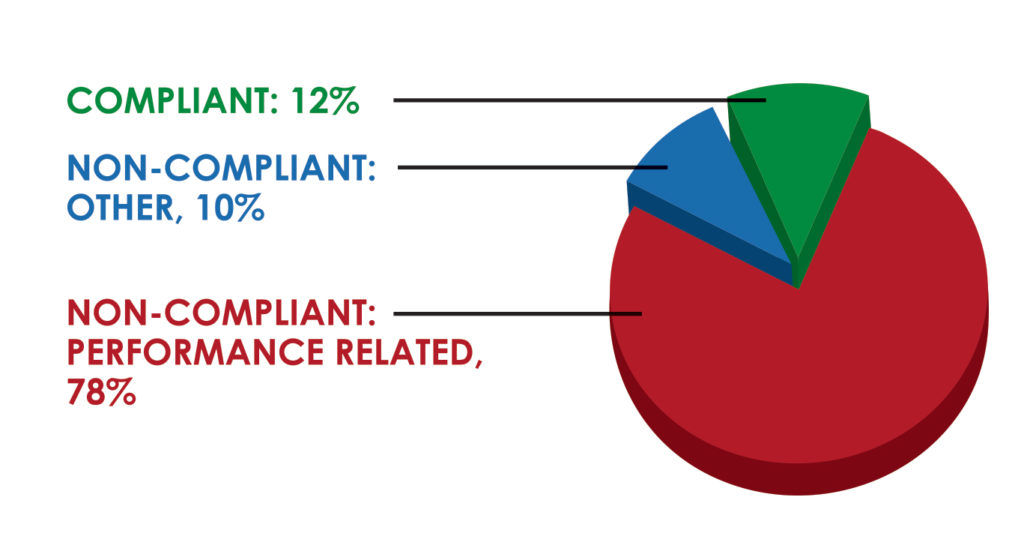
We are offering you a COMPLIMENTARY full day site inspection of you existing emergency response equipment, regardless of brand. And that’s not even the best part…
Once the physical equipment inspection is completed, we’ll provide you a full detailed report which will include the status of each piece of equipment, an executive summary, and…
A full recommendation report detailing what we recommend you need to do to upgrade your equipment to ensure ANSI compliance!
As if that’s not enough, all you have to do to take advantage of this offering is fill out a form! Then, a Haws Representative in your area will reach out to you to schedule the site visit.
Now, how in the world to you pass up an opportunity like this?? You just don’t. So go ahead and hit the pretty green button below to get started! (Restrictions apply)
OSHA Compliance News: Mistakes that hurtOrganization: Felker Brothers Corp., Marshfield, WI.
Business: Pipe manufacturer.
Agency: OSHA.
Penalty: $110,458 (proposed).
Reason for fine: Combustible materials were located within 35 feet of welding activities.
Note: OSHA said wooden racks and form plugs were less than 35 feet away from hot work areas. The employer was also cited because machines designed for fixed locations weren’t securely anchored to prevent them from moving or walking during use. And portable jacks used to support loads weren’t marked with their rated load capacities.
Eyewashes, showers not well maintained.
It’s not enough to just provide emergency eyewash stations and body showers to workers; you also have to make sure the equipment is maintained in good operating condition.
Organization: Eddy Packing Co., Yoakum, TX.
Business: Packing plant.
Agency: OSHA.
Penalty: $128,562 (proposed).
Reason for fine: The company didn’t ensure that emergency eyewashes and body shower stations were maintained according to ANSI standards.
Note: OSHA also said the company didn’t provide fit tests to workers wearing respirators. And staffers weren’t medically evaluated to ensure they could safely use respirators. In addition, the emergency response plan didn’t include information about handling small chemical releases.
OSHA and ANSI Requirements for Eyewash and Safety Showers
[via LabManager.com]
ANSI standard Z358.1 is detailed in terms of defining what is appropriate for safety showers and eyewash stations.
As lab managers and employees, we know that many inorganic chemicals (such as the mineral acids and alkalis) are corrosive to the skin and eyes. Likewise we are aware that many organic chemicals (such as acid halides, phenols, and so on) are corrosive and often toxic. Yet we Safety Guys are continually shocked by laissez-faire attitudes toward the use and maintenance of basic safety equipment by lab personnel, and the resultant unnecessary injuries.
One extreme example we constantly recall is the tragic UCLA accident just a few years ago, which resulted in a fatality from chemical burns.1Â And we recently noticed a post on the American Industrial Hygiene Association pages for Lab Safety Chemical Exposure Incidents, where improper use of an eyewash resulted in a trip to the emergency room.2
The worker was using a fluorescent stain in the cytogenetics lab and felt something splash into his eyes. He was not wearing safety goggles or glasses. (D’oh!) Long story shortened, he flushed his eyes at the nearest eyewash, but they remained irritated and began to swell shut, necessitating a visit to the emergency room. Back at work a few days later, he noticed a coworker using the same eyewash to clean glassware and stainless steel trays, which were left resting in the sink in a cleaning solution. (What?!)
What does OSHA say?
In 29 CFR 1910.151 Medical Services and First Aid, it states that “where the eyes or body of any person may be exposed to injurious corrosive materials, suitable facilities for quick drenching or flushing of the eyes and body shall be provided within the work area for immediate emergency use.”3 OSHA doesn’t provide more specifics regarding what constitutes “suitable” or how “immediate” is defined. So how do we know if we are meeting the intent of the law?
Fortunately, we have the American National Standards Institute (ANSI), and their consensus standard Z358.1, last updated in 2014. This ANSI standard is very detailed in terms of defining what is appropriate for safety showers and eyewash stations. In fact, OSHA uses this reference as a guide when inspecting facilities. So let’s review what is “recommended” for acceptable safety equipment.
Safety shower specs
Begin by checking your facilities for the proper hardware, as recommended by Z358.1. Rest assured that OSHA will, should one or more agents show up for an inspection. For safety showers, the shower head must be capable of flowing 20 gallons per minute (gpm) at 30 psi and producing a 20-inch diameter spray pattern at 60 inches above the surface where the user stands. The center of the sprayhead pattern should be at least 16 inches from any wall, door, or obstruction. It is recommended that the shower head be mounted between 82 and 96 inches off the floor, with the valve no higher than 69 inches.
Eyewash specs
Eyewash stations target just the eyes and therefore have a lower flow requirement. ANSI Z358.1 recommends a flow of 0.4 gpm also at 30 psi. The nozzles should be at least six inches from any obstruction and mounted between 33 and 45 inches above the floor. An eyewash gauge should be used to verify and test the flow pattern.
Requirements for both
Both safety showers and eyewash stations must be able to provide the recommended flow for at least 15 minutes. This usually translates into having the equipment plumbed in with hard connections to the water supply. For example, a quick calculation for the safety shower at 20 gpm yields 300 gallons needed. Self-contained or personal wash devices are allowed, but they are considered supplemental units that can provide immediate flushing while transiting to the permanent fixture.
If the local climate presents potential for freezing conditions, the equipment must be designed to avoid freezing or protected against that situation. Activation valves must open within one second and remain open until intentionally closed or turned off. It goes without saying that these safety devices should be constructed of corrosion-resistant materials.
The 2014 update to Z358.1 added two important criteria. The first is that the requirement for tepid water is now defined as having a temperature of between 60 and 100 degrees Fahrenheit (15 to 37 degrees Celsius). The second change addresses simultaneous operation for combination units. This means that if you have a drench shower combined with an eyewash station, both devices must provide adequate flows and be fully operable at the same time.
Finally and most importantly, consider the location of equipment. We know you have the 10-second rule etched into your brain, as that is the most critical element when it comes to safety showers and eyewashes. This means that travel to the unit should be under 10 seconds for all hazardous areas that need this equipment. This equals about 55 feet. In addition, the drench shower or eyewash must be on the same level as the hazard and have a clear path for travel. We recommend painting or marking the floor area underneath the shower to help keep it clear. Z358.1 also recommends equipment be installed in a brightly lit area and marked with a highly visible safety sign.
Maintenance and training
The last thing you want is to rush to the eyewash or shower, only to be drenched with nasty, sediment-laden water. ANSI recommends flushing all equipment weekly to verify proper flow, and clearing the plumbing of any deposits. If your facility does not have floor drains installed, remember to bring a large, plastic trash can to catch the water. The weekly flushing can also provide a great training opportunity to refresh the operation and travel paths for your employees.
If you want to find out about the ANSI/ISEA Z358.1 significant requirements, attend our free 1-hour webinar on September 21st, 2017.
Register now and become subject matter experts of your emergency eyewash and shower equipment including weekly and annual testing. Request a certificate of attendance after the webinar.
This free webinar will cover:
• ANSI/ISEA Z358.1 significant requirements
• Important 2014 revision highlights
• Compliance best practices
• Live Q&A
WHAT:Â All You Need to Know About ANSI Z358.1Â Webinar
WHEN: September 21, 2017 from 10am-11am PT / 1pm-2pm ET
PRESENTER: Justin Dunn, Product Specialist/Trainer and Samantha Hoch, Marketing Strategist
HOW:Â Register for free
Attendees will receive these complimentary materials after the webinar:
• OSHA white paper
• Weekly and Annual ANSI Checklist
• Access to On-Demand Webinar
References
1. “tert-Butyllithium Claims Fellow Chemist at UCLA,” Chemistry Blog, January 19, 2009, http://www.chemistry-blog.com/2009/01/20/tert-butyllithium-claims-fellow-chemist-at-ucla/.
2. “Lab Safety Chemical Exposures Incidents,” American Industrial Hygiene Association, https://www.aiha.org/get-involved/VolunteerGroups/LabHSCommittee/Incident%20Pages/Lab-Safety-Chemical-Exposures-Incidents.aspx.
3. “Medical Services and First Aid,” US Department of Labor, Occupational Health and Safety Administration, https://www.osha.gov/pls/oshaweb/owadisp.show_document?p_table=STANDARDS&p_id=9806.
Safety Tip: Equipment Location Installation – Defining ObstructionsIf it only takes a single hop, skip, or jump to get to a piece of emergency equipment from any location in your workplace, your workplace is in compliance with one of the ANSI Z358.1 requirements. A walk to the nearest emergency equipment location should total less than 10 seconds and be obstruction free. But what defines obstruction?
Our definition of obstruction is not limited to obstacles or barriers (pipes, closed doors), it also includes impediments or delays (stairs, curbs). An obstruction would be anything that impedes access to the equipment by increasing the time to reach the unit or causing further injury. There are obvious obstructions that would clearly delay access to an emergency response shower unit in 10 seconds or less but other hazards could not only cause a delay but could cause further injury. Stairs (because of the requirement to be on the same level as the hazard), piping, boxes, cabinets, trash, office furniture, etc would all be considered a clear obstruction and should be cleared from the equipment area.
Doors are specifically discussed in the appendix of the standard which is not part of the standard but serves as a guide. The standard states that if a door is used, it must open in the direction towards the shower. Yet, a typical door that opens with a handle would not be accepted per the appendix. Ideally a shower unit that is enclosed will have saloon-type doors that swing in and out for access and don’t require the added motion and added time of twisting a handle. If a door is needed for privacy or temperature control, it must open in the direction of the shower without any type of handle to open the door.
Considerations for equipment location should go into effect before purchasing and installing. It’s important to keep in mind where each individual piece will be stationed and how many pieces will need to be purchased to make sure you are creating a predictable, reliable, stable environment to reduce any unnecessary emergency response problems or delays.
To stay up-to-date on additional safety tips, watch the ”Haws Presents ANSI Z358.1 Answered” on-demand webinar by clicking here.
ANSI Z358.1 FAQ’S: eyewash or eye/face wash? OSHA or ANSI?Casey Hayes, Director of Haws Integrated™, is our go-to expert for questions on ANSI Z358.1. For your quick reference, Casey has responded to your most frequently asked questions to help you stay up-to-date on ANSI compliance.
What is the difference between an eye/face wash and just an eyewash?
An eyewash is specific to eyes, and the water flow rate is designed to hit only the eye surface. It is imperative that the eyewash temperature be 60° – 100° F and have a continuous flow for a full fifteen minutes. Having an eyewash with the right requirements will not only make a difference between temporary blindness and permanent blindness, but increase productivity. Nearly 2,000 eye injuries occur each day in the workplace and with only half of U.S. workplaces in compliance, the cost of an injury can be significant.
An eye/face wash will cover the eyes and a portion of the face. In addition, an eyewash has a .4 gpm minimum flow rate and an eye/face wash has a 3.0 gpm minimum flow rate.
Eye/face washes are beneficial because it’s rare that a victim only has a chemical hit the eye area so using an eye/face wash to flush more of the exposed area will only increase and enhance the emergency response.
Does OSHA use the ANSI standard?
 OSHA requires the employer to provide suitable facilities for quick drenching or flushing of the eyes. While OSHA has not formally adopted ANSI Z358.1, they refer employers to the standard as a source of guidance. In other words, OSHA agrees to enforce safety standards presented by ANSI, while ANSI acts as an assistant to OSHA with safety and health standards. ANSI is recognized as an approval agency of voluntary national consensus standards.
It is the employer’s responsibility to assess the particular conditions related to the needs of the site to ensure the eye/face wash and shower unit(s) provide suitable protection for employees.
For more questions regarding ANSI Z358.1, read our white paper here.
ANSI Z358.1 FAQ: What is the Weekly Test vs. the Annual Test?Are you unsure of when you should test the emergency showers and eyewashes in your facility? Do you know the difference between the weekly and annual testing requirements? In certain cases, a full 15-minute drench period is not required, however it is important to know what is required on a weekly basis versus annually.
ACTIVATE WEEKLY
Per the ANSI Z358.1 standard, you are required to activate the emergency equipment weekly to verify operation and to ensure there is a flushing fluid supply and clear the supply line of any sediment build-up that could prevent the flushing fluid from being delivered due to stagnant water.
How long do you activate for? ANSI states the duration of the weekly activation depends on the amount of water contained in the unit itself and all sections of pipework that are not a part of a constant circulation system, also known as the “dead leg” portions. The goal of the weekly activation is to flush out the stagnant water in the dead leg completely.
TEST ANNUALLY
All emergency eyewashes, eye/face washes, showers and combination units are required to be fully inspected annually to ensure conformance with the installation section of the Z358.1 standard for that type of equipment. The following some of the requirements that need to be met for the annual test:
- The equipment must be assembled and installed in accordance with the manufacturer’s instructions, including flushing fluid delivery requirement.
- Equipment must be accessible within 10 seconds, located on the same level as the potential hazard, and must be free of obstructions that may inhibit immediate use.
- Must be identified with well-lit, highly visible signage.
- Equipment must be connected to a supply of flushing fluid that can produce the required flush time of a full 15 minutes.
- Where the possibility of freezing conditions exists, equipment must be protected from freezing or freeze-protected equipment must be installed.
- Must deliver tepid flushing fluid for the full 15-minute drench period.
- Equipment must go from “off” to “one” in one second or less.
- Must provide a controlled flow of flushing fluid at a velocity low enough to be non-injurious to the user.
How long do you activate for? As stated above, you need to ensure the equipment is is delivering tepid flushing fluid for a full 15 minutes.
For full detailed information on the ANSI Z358.1 requirements for Emergency Eyewashes and Showers, watch the FREE on-demand webinar HERE.
For more ANSI resources such as a testing checklist, click here.
Things to Consider When Choosing Emergency Showers and EyewashesBy Jim Schneider, Plumbing Engineer Magazine
In many work environments, properly installed and utilized emergency fixtures can mean the difference between a minor injury and a major injury or worse. When health and safety is on the line, it’s important to make sure all necessary considerations are taken into account when facilities are being designed and built.
Plumbing Engineer recently spoke to Margo Mee, Product Manager at Haws Corp., about things to think about when choosing emergency fixtures and systems.
PE: Can you tell us about Haws’ background with emergency fixtures?Â
MM: Haws invents, manufactures and builds drinking fountains and standardized and customized emergency response products. For all our products, we continually focus on quality, service, reliability and complete solution support just as we have done for more than 100 years.
PE: What are some of the primary considerations when selecting emergency fixtures?
MM: When researching and purchasing a unit, a product that mimics medical protocols, offers full ANSI compliance in all scenarios, and really considers victim needs and comfort is the ideal solution to offer a complete emergency response system.
PE: From the manufacturing side, what are some of your primary considerations when designing and making emergency fixtures?
MM: Victim comfort for maximum results is the primary consideration when designing emergency products, but it also important that the product is reliable and durable. Our quality products are thoroughly tested and evaluated at numerous points during design and build.
PE: What kinds of challenges do you face with emergency fixtures? How do you deal with those challenges?
MM: Because they are not used frequently, a lot of facilities will place their importance on the back burner and not evaluate if their site’s needs have changed, if the install location is still ideal, if the units even work or are ANSI compliant. The best way to address these common issues is through continuous education. We offer onsite facility testing and evaluation, detailed informational videos, and on-demand and live webinars with access to our engineering team.
PE: Has the standard and market for emergency fixtures remained pretty constant, or are there many updates and changes?Â
MM: The last major change in the standard was in 2009. That revision included a definition for tempered water and from there you could see product changes. The market itself continues to grow as people are more educated and are asking the right questions and demand that their site provide the ideal solution. Manufacturers are held accountable for providing a reliable product and if they can’t adhere, their products are being replaced.
PE: Are there any trends or updates to the standard you see on the horizon?
MM: We would hope to see a revision in the next 6-12 months.
PE: You wrote a white paper about exceeding the ANSI Z358.1 Standard. Can you tell us a little about the baseline of the standard itself?
MM: The ANSI Z358.1 Standard defines emergency eyewash and shower design, location, testing, activation, and temperature requirements for proper functionality and usage. Simply providing emergency eyewash and shower products is not enough. Facilities must inspect, test, and monitor emergency equipment system readiness and performance. Even though the most current ANSI Z358.1 standard now dates to 2009, most emergency eyewash and shower units across North America still do not yet comply with these significant provisions.
PE: Why should end users be looking to exceed the standard?
MM: Treat the situation as if you could be a victim. You would only want the best solution that performs as required as well as provides an additional benefits so the emergency response tool doesn’t cause further injury.
PE: How can products and systems exceed that standard?
MM: Haws products go beyond the minimum performances of emergency eyewashes and showers requirements by keeping the victim in mind when in an emergency situation. Haws products include victim comfort with water pressure and flow, effective flushing with the use of our unique AXION directional flow, appropriate and recognizable color coding, and temperature controls to encourage proper usage. In addition, Haws offers a variety of educational tools to help educate and train users.
Preparation: The Best Guard to an Emergency
Do you know the protocol to flushing hazardous chemicals off of your body in an emergency? It’s always a good rule of thumb to be knowledgeable on how to properly execute safety shower and eyewash performance in an emergency situation. Take the time to get to know the mechanics of the emergency equipment in your facility before an accident takes place. Casey Hayes, director of Haws Integrated™, recommends the following:
- Get a proper training session on emergency equipment. Be aware of the location of the unit and how long it takes to arrive at the unit from your work space.
- Confirm that it should not take more than 10 seconds to arrive to the emergency equipment.
- Upon arrival to the shower, pull lever and remain in shower for a full 15 minutes. This is to ensure the prevention of chemical absorption while it also helps to cool burns and prevent hypothermia.
- When using an eyewash or eye/face wash, hold eyes open during the entire 15 minute flushing period.
- In some cases, it may be appropriate to have a partner with you during the state of emergency. If you work alone, you may not have the opportunity to have someone assist you. We recommend that if you are in a state of shock, have a co-worker assist you to the emergency shower and or eyewash station. If you are saturated in chemicals, it is best not to expose anyone else and to proceed to the emergency station alone.
- Always go to the emergency room following the use of the emergency shower and/or eyewash.
Furthermore, it’s essential to have functional emergency showers and eyewashes throughout your facility. Refer to our previous blog post ANSI Z358.1 FAQ: What is the Weekly vs. Annual Test for a break down on when it is appropriate to perform each test. We also offer a free webinar on the requirements for emergency eyewashes and showers. Click here to watch.
Increase In OSHA Fines Now in Effect
For the first time in twenty-five years, OSHA penalties are increasing – and significantly. A federal act passed in 1990 exempted OSHA from increasing fines to account for inflation, but the new budget signed into law on November 2, 2015, includes an amendment striking that exemption.¹
The “Catch-Up Adjustment,” based on the percentage difference between October 1990 and the Consumer Price Index Budget of October 2015, will amount to a penalty increase of about 80%. That will bump the current $7,000 cap on serious OSHA violations to about $12,500, and the willful, repeat violations penalty of $70,000 to just over $126,000. Once this one-time adjustment is made, OSHA will also be required to adjust penalties annually using the Consumer Price Index’s yearly percentage increase.²
Budget changes will go into effect on July 1 of 2016, and increased penalties will begin August 1 in all states regulated by OSHA. For employers, now is the time to ensure that workplace safety programs and equipment are meeting appropriate standards. This includes:
• Confirming that employee safety training is comprehensive and documented
• Assessing workplaces for potential hazards and addressing them in the most appropriate manner
• Addressing employee safety concerns
• Confirming that existing safety equipment is fully compliant and operational
Consider the OSHA penalty hike a boon for workplace safety. Studies have shown that workplace injuries are reduced in settings in which health and safety inspections have direct consequences for violations.³ And while it can be asking the impossible to build a system with the resources to inspect every single workplace for violations, increasing employer awareness about steep financial penalties for non-compliance may well do the trick. An 80% increase in current OSHA fines will likely prove an effective method of stressing the importance of workplace safety.
Interested in learning if your facility is ANSI compliant? Sign up for a complimentary, one-day onsite ANSI Survey at www.Hawsco.com/survey.
TO DOWNLOAD THIS WHITE PAPER, CLICK HERE.
¹OSHA fines to increase significantly. (2015, November 5) Retrieved from http://www.safetyandhealthmagazine.com/articles/13258-osha-fines-to-increase-significantly
²Employers beware: OSHA fines are on the rise for the first time in twenty-five years. (2015, November 11). Retrieved from http://www.oshalawupdate.com/2015/11/11/employers-beware-osha-fines-are-on-the-rise-for-the-first-time-in-twenty-five-years/
ÂłInspections with penalties linked to lower injuries: IWH review. (n.d.)Â Retrieved from http://www.iwh.on.ca/at-work/81/inspections-with-penalties-linked-to-lower-injuries-iwh-review
Top 12 Non-Compliance Issues in Emergency EquipmentThere are two types of non-compliance when referring to emergency shower and eyewash equipment.
A. Performance Related:Â Any type of issue that affects the ability for the emergency shower or eyewash to provide proper first aid in the event of an emergency. This could include lack of tepid water, insufficient flow to the showerhead, eyewash heads or both, too much flow or pressure to the heads, or a combination unit that does not have the capability of providing adequate flow to both the showerhead and eyewash heads simultaneously. Failure to meet the requirements in these areas can have a significant impact on the outcome for the victim.
B. Not Performance Related (other): Issues that do not affect the proper functioning of the emergency equipment and the ability to deliver tepid water at the proper flow rates etc. These are considered low-impact non-compliance. Typical examples include missing signs, misplaced or missing dust covers, minor deviations in installation heights, obstructions in the pathway to the equipment, and failure to conduct weekly inspections. These issues may not affect the ability of the equipment to deliver proper first aid so they are considered “non-performance” related reasons for failure to be in compliance with the ANSI requirements.  Although seemingly minor, these issues will be cited by OSHA and still need to be corrected.
To highlight, we have identified the top 12 most common reasons emergency showers and eyewashes do not comply with the standard.
NON-PERFORMANCE RELATED
#1: Improperly installed or missing dust covers
This exposes the nozzles or outlets to airborne contaminants which can ultimately make their way into a victims eyes and exacerbate the issue.
#2: Lack of proper signage on the equipment or lack of acceptable lighting
Although this does not affect the unit’s ability to perform, it can prevent a victim from finding the shower or eyewash during an emergency.
#3: Providing the improper equipment for the application
Meaning that maybe an eyewash has been installed when an eye/face wash is the correct solution.
#4: Obstructions in the path of travel to a shower and/or eyewash
Examples include hosing, boxes, and other equipment. This could prohibit a victim from being able make their way to the equipment, thus inhibiting its use or possibly leading to a trip or fall and the risk of further injury.
#5: Improper installation of eyewash nozzles, actuators and showerheads
Incorrect placement or assembly could result in an inadequate emergency response thereby potentially causing further injury.
These next 7 reasons for non-compliance are considered performance related, affecting the ability of the unit to provide proper first aid.
PERFORMANCE RELATED
#6: Parts of a unit, such as the pull rod or push flag, in a dysfunctional, non-usable state
This could create a situation where a victim is unable to use the equipment if needed. This is a very common issue we have witnessed in the field.
#7: Lack of flow control to the eye or eye/face wash including erratic, inconsistent or unpredictable water flow
From an independent study of practicing ophthalmologists, comfortable water pressure is important and should be provided to a victim with the expectation that they will be flushing for a full 15 minutes. This is commonly seen pertaining to showerheads as well.
#8: Insufficient water pressure or flow rate
With not enough water pressure or flow, the eye, eye/face wash and/or shower can be considered unusable and may not provide proper flushing capabilities to a user with chemicals or harmful substances on their body.
#9: Uneven flow patterns
The eyewash is not capable of providing flushing fluid to both eyes simultaneously. This is considered non-compliant as the standards requires that a controlled flow be provided to both eyes.
#10: Improper alignment
Regarding combination units, the second most common compliance issue is improper alignment. Many times, the showerhead is not in alignment with the eye or eye/face wash and vice versa, thus not allowing for simultaneous use of the shower and eyewash by the same user.
#11: Does not maintain flow rates for simultaneous use when shower and eyewash are both activated
The most common reason for non-compliance is the inability of the equipment to maintain the required flow rates when both the shower and the eye/face wash are activated at the same time – a requirement of the standard since 2009. Although the eye/face wash may meet all flow requirements when activated alone, once the shower is activated, the flow to the eye/face wash is often impacted, making the unit no longer compliant – and more importantly, impacting the ability to deliver proper first aid, putting the victim at risk.
#12: Not providing tepid water
As of 2004, the ANSI standard incorporated the tepid water requirement, yet many existing and new units have yet to comply. All showers and eyewashes must provide tepid water in between 60-100 degrees Fahrenheit or 16-38 degrees Celsius.
ARE YOU COMPLIANT? 88% OF UNITS SURVEYED DO NOT MEET THE CURRENT ANSI Z358.1-2014 STANDARD.
If you believe any of you equipment is non compliant, now is the time to fix it. Take advantage of our Complimentary ANSI Site Survey Program. Fill out the form here and you will be contacted to set up a onsite review of your emergency equipment. Following the site visit, you will receive:
- INSPECTION REPORT (PDF):
Fully detailed report on each piece of equipment and its current status, regardless of brand or model. - Â EXECUTIVE SUMMARY CHART:
Comprehensive overview of findings. - Â RECOMMENDATIONS:
Detailed summary of key observations, potential root causes, and recommendations. - DEBRIEFING MEETING/WEB CONFERENCE:
Interactive meeting to discuss best practices and proposed solutions to any deficiencies identified.
UP TO 1 FULL DAY OF INSPECTIONS ON EMERGENCY SHOWERS AND EYEWASHES INCLUDED
Let our Haws professional representative’s help you mitigate risk and ensure compliance.
SIGN UP NOW!
OSHA and ANSI Z358.1: Your Guide to Compliance
Your Guide to ANSI Z358.1 Compliance
DATE: JUNE 23rd, 2016
TIME: 10:00-11:00am PT/ 1:00-2:00pm ET
DESCRIPTION: In November 2015, it was signed into law that OSHA fines are increasing by 80% for the first time since 1990. Ensure you are complaint with the updated ANSI Z358.1 Standard to avoid fines and guarantee you are providing properly functioning emergency equipment.
Hosted by leading ANSI compliance field expert Casey Hayes, this free web seminar will cover:
• ANSI Z358.1-2014 revisions and significant requirements
• Compliance best practices
• Live Q&A
Attendees will receive:
• Complimentary OSHA white paper
• ANSI checklist
• Access to on-demand webinarÂ
Questions answered by ANSI subject matter expert and Director of Haws Integrated Operations, Casey Hayes.
Is testing of the safety showers and eyewashes actually required in the standard and not just the appendix?
Yes, it is part of the standard. It is not in the appendix. We talk about the weekly flush and the requirements to get the debris out and to ensure that water is available. And, we also discuss in the standard the requirements for the full ANSI annual test. The annual test ensures things like making sure we have 20 gallons per minute to the showerhead and that the spray pattern of the shower meets the requirements. Same for the eyewash. It is also when you will test to make sure it is 10 seconds from the hazard and nothing is obstructing the pathway of victim reaching the unit.
2. Does the accessible 10 second rule apply to a fast pace walk or run?
In previous revisions, there was a distance in the requirement. At one point, we had 10 seconds and 100 feet. At another point, we had 10 seconds and 55 feet. We have taken out the distance requirement so that we don’t have to determine whether it is a walk or a run. We are putting that back onto the installation aspect for you to determine what 10 seconds looks like. In the appendix, it does talk about 55 feet which is probably the right distance, but the standard does not get into the details.
3. Does EPA prohibit floor drains in college chemistry labs?
I have never been asked about this as far as EPA. I do know that the ANSI Z358.1 standard is strictly a performance standard and does not talk about floor drains because they are concerned about the performance of the shower. So, floor drains have nothing to do with that. If you look at plumbing codes, it specifically says that floor drains are not required. We believe that is due to the fact that they don’t want water that has chemicals in it to go to the sewer drain. I have never seen anything related to EPA.
4. Can you please reference the OSHA standard that requires testing once a week?
CAL OSHA says they only enforce once per month. OSHA specifically does not talk about anything in regards to the performance of the safety shower. It specifically says it must supply a suitable facility. It does not get into specifics as to what a suitable facility is. OSHA is starting to reference the ANSI standard as a guideline as to what a suitable facility is but nowhere in OSHA do they talk about the testing of the equipment. If you are building to the plumbing code, specifically references that the shower must meet ANSI and therefore the requirement for weekly/annual testing comes into play.
5. Are written records of testing required on-site?
This is outside the ANSI standard. This is what I would call a best practice. We are seeing that the testing validation is not on the tag on the shower but not being placed with the health and safety time. Testing has been enhanced so people are collecting and filing it away.
Learn more about ANSI by registering for our upcoming live web seminar on ANSI Z358.1-2014 Compliance.