Visit us at the upcoming IFMA (International Facility Management Association) World Workplace 2018 Expo, Oct 3-4 in Charlotte, NC.
Your expo badge is on us but don’t forget to visit our booth #1231.
GET YOUR FREE BADGE NOW>>
Emergency Eyewashes & Showers: Q&A with ANSI ExpertAnswers provided by Justin Dunn, Haws Product Specialist / Trainer
How often do I have to test my showers and eyewashes?
Testing is required on both a weekly and annual basis. Weekly test consists of a quick on/off “bump” test to ensure water flow to the equipment and clear out the dead leg in the supply line. An annual test is a full 15-minute performance test measuring the entire unit against the ANSI Z358.1 standard.
How can I fix flow issues without having to replace the full shower and eyewash unit?
This is easily done using our AXION Advantage retrofit kits that can fix the most common issues with emergency equipment including simultaneous flow, uneven flow rates, and injurious flow rates. Our kits can retrofit old Haws models as well as 80% of our competitor’s units helping to bring them back into compliance.
What is the OSHA Standard for showers and eyewashes and do they use ANSI?
The OSHA standard is 29 CFR 1910.151 (c) and states “where the eyes or body of any person may be exposed to injurious corrosive materials, suitable facilities for quick drenching or flushing of the eyes and body shall be provided within the work area for immediate emergency use”. OSHA references the ANSI Z358.1 standard as the primary source for compliance and will often issue fines using the standard.
How do I know what to check on the weekly and annual test?
You can do this by one of three methods: (1) Use the complimentary Haws ANSI checklist created specifically for weekly and annual testing compliance using the Z358.1 standard, found HERE, (2) watching a step by step video on how to test, found HERE, or (3) taking our 25 minute online competent inspector training course that will certify you for 2 years to conduct the weekly and annual inspections accurately. Only $49.99, found HERE.
Is there a company that will come and test all my units for compliance?
Haws offers a FREE 1-day shower and eyewash site survey for sites that qualify. A trained and experienced representative will visit your site and measure your equipment against the ANSI Z358.1 standard for any non-compliance issues and even provide solutions to help bring you back into compliance. You can find out if you qualify HERE.
Contact Justin Dunn:
[email protected]
775.353.8396
This nationwide event is taking place Aug. 13-19, 2018. Led by OSHA, Safe + Sound Week is meant to raise awareness and understanding of the value of safety and health programs that include management leadership, worker participation, and a systematic approach to finding and fixing hazards in workplaces. What are you doing to make your workplace as safe as can be? Want to see what others have done in the past? Click here to view a webinar put out by the US Department of Labor on YouTube.
Participant Numbers by State
Complimentary Site Survey of your Eyewashes and ShowersHave emergency showers and eyewashes in your facility? Do you know if they are compliant with the most recent ISEA/ANSI Z358.1- 2014 Standard?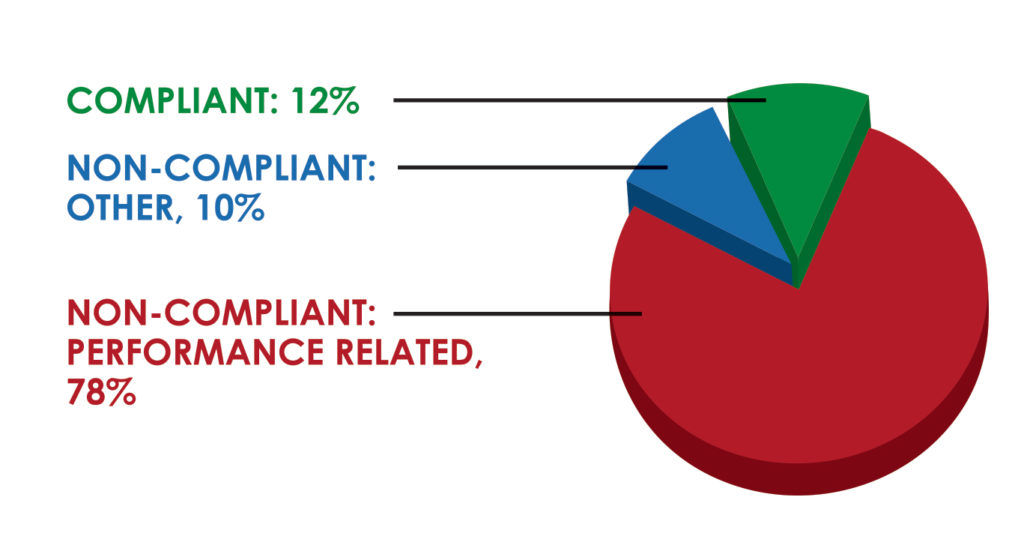
We are offering you a COMPLIMENTARY full day site inspection of you existing emergency response equipment, regardless of brand. And that’s not even the best part…
Once the physical equipment inspection is completed, we’ll provide you a full detailed report which will include the status of each piece of equipment, an executive summary, and…
A full recommendation report detailing what we recommend you need to do to upgrade your equipment to ensure ANSI compliance!
As if that’s not enough, all you have to do to take advantage of this offering is fill out a form! Then, a Haws Representative in your area will reach out to you to schedule the site visit.
Now, how in the world to you pass up an opportunity like this?? You just don’t. So go ahead and hit the pretty green button below to get started! (Restrictions apply)
How Safe Are Drinking Fountains in NYC?Clean water has been a topic of both national and local concern in recent years. Flint, Mich., famously made headlines in 2014 for its dangerous, lead-tainted water supply — a major threat to children’s brains and nervous systems, as well as adults’ reproductive systems.
People disparage drinking fountains all the time, but they provide a needed service for all of us  – providing water to stay hydrated. Recently The New York Post tested water fountains in the most frequented parks in NYC, and found that all met or exceeded the state’s guidelines for water quality. New York City has a reputation for having the “highest quality” tap water and this testing only helps to verify that.
Happy Independence Day from Haws! New Specification Tools Now Available!
Visit our new Spec Tools Resource Page on Hawsco.com that houses Haws’ new 3 part specs from MasterSpec for Drinking Fountains and Emergency Equipment, as well as access to Revit files on BimObject.com and CadDetails.com.
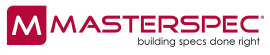
Visit our MasterSpec® page.
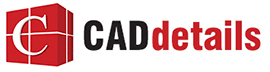
Visit our CADdetails® page.

Visit our BIMobject® page.
Irrigate eyes like medical pros [First seen in ISHN Magazine June 2018]
Introduce the flushing fluid at the inner corner of the eye
An injury can change life in an instant. According to the National Safety Council, occupational injuries occur every seven seconds in the United States. Luckily, through the years, stringent regulation and a growing concern for the health and well-being of employees has led to advancements in processes, safety procedures, and first aid protocols to treat the injured. This movement has had a profound impact on emergency equipment, including the eyewash industry.Â
In the early 1900s, it was said that a well-known energy company created the first emergency eyewash by taking two bubbler heads from drinking fountains and mounting them on opposite sides of a sink facing each other with plumbing run to both of the heads (see photo). When activated, the water streams formed a double arch that directed water from the outer perimeter of the sink to the center. An injured victim would place their face into the double streams and irrigate both eyes simultaneously. It was a great concept and one that took the safety industry to a new level over the subsequent years.
Yet, as medical advancements continued to evolve, the eye irrigation process in emergency situations did not quite follow suite. Irrigating with water streams that contact the eye at its outer corner, or canthus, and flow inward toward the nose is diametrically opposed to the way medical professionals irrigate eyes.
Think about how you use eye drops. The general practice is to tilt the head back and place the dropper near the inner corner for the drops to drain to the outside of the eye and down the outside of your cheek.
The Lacrimal System
To comprehend the logic behind how the medical communitytreats eye contamination situations you first should understand the eye’s lacrimal system. The human eye is equipped with an automatic lubricating and cleansing mechanism, called the lacrimal system (see illustration). It consists of the lacrimal gland which produces tears, the ducts that channel tears from the lacrimal gland to the ocular surface, and the lacrimal puncta which are drains that channel excess fluids out of the ocular surface.
Importantly, the lacrimal puncta drain excess fluids directly into the nasal cavity. This process is the reason why your nose runs when you cry.
The eyelid also plays a key role. As we blink, the eyelid wipes the cornea pushing contaminants and excess fluids toward the lacrimal puncta – or the ocular surface’s drains.
If a hazardous substance is introduced into the eye, nature’s own cleansing mechanism can serve to force the contaminant into the nasal cavity, where it can be breathed into the lungs or swallowed.
Eye irrigation: The medically consistent way
The medical profession teaches and practices irrigating eyes by introducing the flushing fluid at the inner corner of the eye – adjacent to the nose – and letting it run across the eye to the outer edge. In effect, irrigation is performed by moving the fluid away from the lacrimal puncta. This is opposite the flow direction of traditional eyewash products that flow water from the outside-in, pushing contaminants toward the inner corners of the eyes where these susceptible tear ducts, glands and canals are located. Pushing contaminants toward the nose not only risks introducing them into the nasal cavity, but also can allow the same contaminant to be introduced into the other eye.
The ideal method of irrigating eyes in any use is by using products that mirror approved medical protocols. Eyewash streams that are inverted contact the eyes at the inner canthus, or corner, adjacent to the bridge of the nose. Contaminants are thus swept away from the lacrimal system to the outside of the eye where gravity takes over and runs them into the eyewash bowl (see image). This added protection to valuable internal organs helps reduce unnecessary exacerbation of injuries.
Consistent laminar flow for victim comfort
Additionally, the use of laminar flow design in the eyewash streams is another medical recommendation. A laminar flow is one in which there is an absence of turbulence, because the stream is “built” in layers. Turbulence or inconsistencies in the flow stream can strike the eye as a change in total pressure, making the victim much less comfortable during the flushing process and less likely to stay in the water for the required duration. The best approach is to provide an even, comfortable, predictable stream height and circumference, accomplished by using laminar design principles.
Times are changing, as are the protocols and practices of emergency equipment manufacturers. Irrigating eyes in a manner that is consistent with medical procedures provides the ideal situation for a victim from a comfort and effectiveness standpoint in a circumstance that may not be so ideal.
Safety Equipment on College CampusesBy: Joanne Benz, Haws
Injuries caused during a chemical spill back in 2016 at Sacramento State College set off an alarm with officials at the California State Auditor’s office. The California State University Chancellor’s Office claimed that it does not consider itself as an oversight entity responsible for health and safety, but instead provides guidance, resource materials and collaboration. Most college campuses use hazardous material for instruction and research. Students and employees can be exposed to chemicals in laboratories, classrooms and stockrooms. The Auditor also found that campuses do not always conduct regular inspections of safety equipment such as emergency showers and/or emergency eye washes. After the auditor found that 46% of the 23 California State Universities do not seek input when assessing risk to employ health and safety in chemical stockrooms or laboratory areas. Since the audit, the CSU Chancellor’s office and university officials involved concurred and said they will comply with the auditor’s recommendation. The Chancellor’s Office now plans to conduct health and safety audits at all 23 campuses beginning in 2019.   Four CSU Sacramento employees filed an $80 million claim against the university over the chemical spill.
Haws® Services is a warranty and service provider for all brands of emergency shower and eye/face wash products to ensure your emergency equipment is ANSI compliant and functioning properly. From startup and commissioning to annual inspections and preventative maintenance, Haws Services‘ experts specialize in emergency response equipment.
Learn more about our service offerings here. We take the burden off you and your employees so that you can rest assured that students and faculty get the help they need when they need it.
Six Sigma and Safety: Using Data to Improve OutcomesSix Sigma is a set of tools and processes designed to reduce defects and improve processes. Introduced by Bill Smith from Motorola in 1986, the Six Sigma system has since been adopted by large publicly traded companies like GE, Amazon, Bank of America, 3M, and more.
A significant portion of Six Sigma practices are designed around reducing defects. Defects in products create costs for companies, so reducing defects can improve the financial performance of manufacturing companies. Six Sigma practices can also reduce production and delivery time by eliminating wasteful actions and focusing on the important elements of a process.
It’s clear that Six Sigma can be used to increase profits, reduce process time, reduce costs, and increase customer satisfaction. But can these systems be used to improve facility safety? How can safety professionals apply Six Sigma processes to keep people safe? If we think about workplace accidents as type of defect and work to reduce them, we can improve our businesses and make people safer.
Six Sigma relies on a process with 5 phases called DMAIC (Define, Measure, Analyze, Improve, and Control):
- Define the system, the voice of the customer and their requirements, and the project goals, specifically.
- Measure key aspects of the current process and collect relevant data; calculate the ‘as-is’ Process Capability.
- Analyze the data to investigate and verify cause-and-effect relationships. Determine what the relationships are, and attempt to ensure that all factors have been considered. Seek out root cause of the defect under investigation.
- Improve or optimize the current process based upon data analysis using techniques such as design of experiments, poka yoke or mistake proofing, and standard work to create a new, future state process. Set up pilot runs to establish process capability.
- Control the future state process to ensure that any deviations from the target are corrected before they result in defects. Implement control systems such as statistical process control, production boards, visual workplaces, and continuously monitor the process. This process is repeated until the desired quality level is obtained.
Let’s take these Six Sigma processes and apply them to safety.
The definition of a system from a safety perspective is simple. You must identify what work is being done and what the desired outcome is. For example, a manufacturing process that aims to add a bevel to a piece of wood ends with an outcome of a beveled piece of wood. The goal is to produce that item as quickly and safely as possible.
The second step in applying Six Sigma processes to safety is measurement. Six Sigma relies on data to improve processes, and collecting the correct data is critical to improving outcomes. At Haws, we collect information about safety incidents in several different ways to ensure we have a complete picture. Our detailed data about safety incidents, near misses, and other metrics are tracked over time. This data can be self-reported by workers in anonymous form collection bins we placed throughout our facility, as well as reported directly to the workers’ supervisor. A standardized data collection form that requires quantitative safety data for submission makes the data easy to spreadsheet, track, and report on. Random safety inspections by our safety team led by Melanie Mayer give us a closer look at processes in the building that require further improvement.
It’s important to collect and monitor safety data over long periods of time. Single data points about safety incidents are important, but do not give you deep insights about potential areas for improvement. In processing data you may find that patterns start to emerge. Perhaps workers are more likely to be injured or have a safety event with a particular tool or piece of equipment. You will only get this insight from long-term data capture. The long-term tracking and processing of safety data will enable a deeper understanding of areas for safety improvement.
Data about safety events, injuries, near misses, and hazards must be processed in a systematic way. A monthly processing of newly collected safety data can provide new insights into potentially unsafe behaviors and equipment. Time-series analysis of data can demonstrate issues on certain days of the week or month caused by external factors, or show that certain equipment must be replaced after a given period of time in order to prevent accidents. For example, you might find while processing safety data that includes the purchase date of equipment that certain hearing protection stops being effective after a period of time due to material degradation, prompting workers to injure their hearing. This kind of finding would never be possible without a complete collection of data that includes the equipment type and purchase date. Be creative and start looking at data that is not necessarily related to the equipment or personnel. You might come to surprising conclusions about how to keep your team safe!
After defining a process, measuring the important attributes, and analyzing the data you’ve collected, it’s time to apply your knowledge. Every safety manager knows that small changes can make a big difference in the health and safety of your team. Start by making small tweaks to your process, whether it’s improving or replacing equipment, changing a process, or giving training.
In order to have conclusive results about the success of your safety improvements, it’s important to isolate the changes so that you can compare your test to your control data. That’s a great time to bring up the fifth step of the DMAIC process: Control. It’s important while making these changes that you document the steps you took and track the same data you were before the changes. This is because making several changes simultaneously can confound the results and make it unclear which of your changes improved your process.
Six Sigma is a valuable system for safety professionals because it provides a solid conceptual framework for making safety changes in a data-driven way. Following the Six Sigma system generates large quantities of useful safety data that will benefit your company and team members for years to come.
New Video! Haws Hydration Products OverviewWant a to learn more about Haws’ Hydration products offering including drinking fountains and bottle fillers? Watch this overview video that outlines the product families offered, features and benefits of Haws, and new products available in the marketplace!
Creating a ‘Comfort Zone’ for Emergency Equipment Water Temperature[via OH&S Magazine May 2018 Issue]
Creating a “Comfort Zone” for Emergency Equipment Water Temperature
By: Samantha Hoch, Product Marketing Specialist at Haws®
Tempered water has been a hot topic of late, but just as many installations need cooling of high-temperature supply water.
Moving water transfers heat, either increasing the temperatures of the objects it contacts or decreasing them. Heat transfer, via moving water, made twentieth century man more productive and more comfortable. It sped up transportation and made a wealth of innovative products possible. But, while the physical properties of heat transfer via water movement can certainly be beneficial, there are many instances when temperatures must be controlled within a high and low range to avoid injury. For many years, industrial emergency equipment was not one of those instances. The water that flowed through emergency showers and eyewashes were subject to climatic, source affected and other ambient variables that could raise it to injurious temperatures or lower it to downright freezing temperatures.
Municipally supplied water, when running for a sustained period, tends to cool down or even heat up, eventually approaching its source point temperature. And, by the same token, water subjected to hot or cold ambient temperatures in manufacturing plants or elsewhere can become dangerously hot or cold. Presently, OSHA – 29CFR 1910.151(c) – requires the availability of suitable first aid treatment facilities. Specific direction is given indicating that “suitable facilities for quick drenching or flushing of the eyes and body shall be provided”.
While the definition of “suitable” was mostly left up to the specifier in the past, the current ANSI/ISEA Z358.1-2014 Standard provides much greater clarity. ANSI mandates a water delivery temperature range defined as “tepid”. This is clarified as a 40-degree temperature range for flushing fluids spanning from 60°F to 100°F [16°C to 38°C]. Yet, no source information proves that 60°F for 15 minutes in potentially freezing outdoor conditions will not lead to hypothermia. Nor is there supporting documentation to verify that 100°F would not scald or further injure the delicate eye tissues or skin.
The thought of an injured worker short-cutting the required emergency equipment use cycle because the water is too cold or hot has led to the notion of the “Comfort Zone”- a revised outlet water temperature range that assures comfortable, non-injurious use for the full 15-minute use cycle.
Revisions to the ANSI/ISEA Z358.1 Standard have occurred on a somewhat routine basis. Published in 1981, the standard was updated in 1990, 1998, 2004, 2009 and most recently in 2014 with the expectation of another update on the horizon. It is suggested that a revised water temperature range between 70°F and 95°F can help ensure medically effective results and provide that best practice comfort zone. Increasing the minimum flushing fluid temperature to 70°F can encourage users to use the equipment for the full fifteen-minute flush cycle, protect against cold shock that could lead to cardiac arrest, and advocate for the removal of contaminated clothing. Decreasing the maximum temperature to 95° F will help avoid temperatures known to harbor specific bacteria growth, prevent scalding of the eyes and skin, and reduce the chances of an increased chemical reaction.
So, how do you ensure a facility’s equipment falls within the comfort zone? For the sake of this discussion, we will assume that the plant has sufficient emergency equipment in the appropriate locations and that the comfort zone approach is being added to the existing emergency equipment assets.
Let’s consider the most appropriate steps to be taken:
- Ascertain your actual inlet water temperature range and compare it to the desired range – This involves checking the initial and sustained temperature readings at the various emergency equipment sites located throughout the facility. Since conditions can change from location to location, the chore of checking each shower and eyewash is the safest bet. Don’t forget the impact of seasonality on water temperatures. It may be necessary to check at several times during the year.
- Determine the overall changes needed – If initial temperatures are either too hot or too cold, while sustained temperatures are within the ANSI mandated temperature range or even the recommended comfort zone, consideration of a re-circulation system is appropriate.
If sustained use temperatures fall outside of the temperature parameters, you may require warming technologies, cooling technologies or in certain areas and circumstances, both. In most instances, these types of systems can be sized to handle multiple showers/eyewashes each. Specific applications should take into account the volume of shower and eyewash locations to be included in each loop, the maximum distance between components and the impact of exposure of warmed or cooled pipes to ambient air temperatures. It is highly recommended that specifiers work with eyewash and shower manufacturers directly to determine the appropriate system, given your specific geographic location, processes, temperatures, and layout/equipment locations.
It should also be noted that while tempered water – meaning warming cold water – has been a hot topic of late, just as many installations need cooling of high temperature supply water. Elevated temperatures can come from several sources, including high ambient temperatures, exposure to process heat or excessively high supply temperatures.
- Identify the number, required location(s) and sizing of the thermostatic mixing valve(s) – This applies only to tempering water or warming sustained use cold input water prior to emergency equipment use. Temperature control for cooling operations is handled integrally within the systems chiller unit.
The brain of a warming system is its thermostatic mixing valve. This device ensures that the safety equipment safely receives water at the required temperature. A good thermostatic mixing valve is actually a system of valves, typically designed by safety equipment manufacturers since they understand their equipment and their specific flow rate requirements. Specifiers are cautioned to do their homework well with respect to selection of the proper valves for your specific needs.
- Determine your hot and/or cold water source – In sizing the tempered water system for any particular application, providing a source for sufficient quantities of water is essential. Recent advancements in instantaneous hot water heaters have made these products practical for use in emergency equipment applications, especially where space for traditional hot water heaters and hot water storage tanks is limited.
- Consider the maximum simultaneous usage – Always work to the maximum use, worst-case volumes. Booster and/or re-circulation pumps, as well as storage tanks, may be necessary to assure the availability of the maximum demand volume of tempered water. A variety of products are available to fill these needs.
The science of emergency equipment design and specification continues to advance rapidly and the clear winners are the specifiers that stay “on top” of the advancements and the employees who are protected by them. Establishing and maintaining a best practice comfort zone for water temperature delivery provides everyone the maximum peace-of-mind.